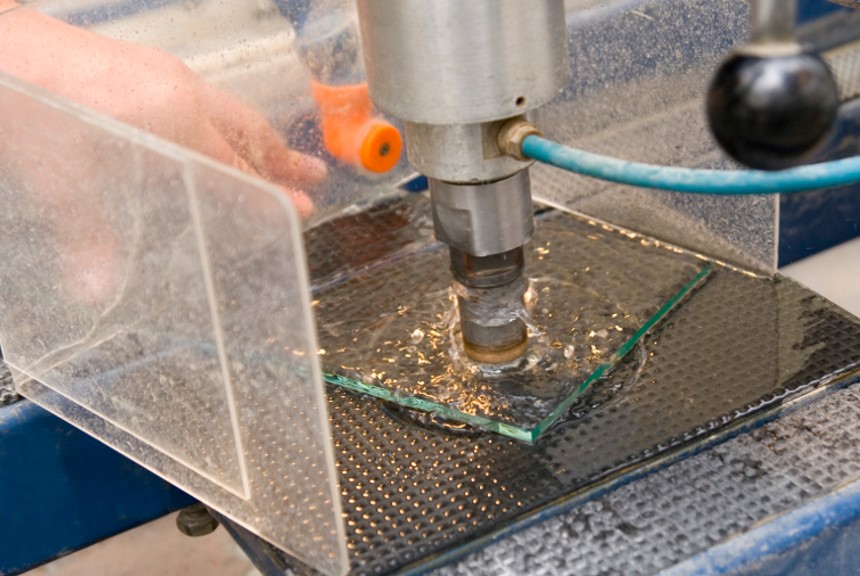
If you operate or maintain machinery, your exposure to unguarded or inadequately guarded machines can cause serious injury or death. This training session on machine guarding includes important information about how to protect yourself against serious injury when working with powerful machines.
By the end of this session, you will be able to:
- Recognize the hazards of working around machinery;
- Identify the parts of machinery where hazards frequently occur and the hazards associated with each;
- Identify and safely use the types of machine guards and safety devices you may encounter in the workplace;
- Follow machine guarding rules and best practices to protect yourself from injury; and
- Operate machines with guards properly.
Table of Contents
Knowledge Check 1
Before we begin, let’s see how much you already know about machine guarding.
- True or False—Amputations are the most common injury caused by machines. – False
- True or False—Machine guards protect both machine operators and other workers in the area. – True
- True or False—You should only remove machine guards when the machine is operating. – False
Machinery Hazards
Every year, workers who operate and maintain machinery suffer tens of thousands of injuries. Cuts, lacerations, and punctures are the most common, but amputations, crushing injuries, fractures, and other severe and disabling injuries affect thousands of workers each year.
- These injuries can even be fatal. According to the Bureau of Labor Statistics, hundreds of workers are killed by hazardous machinery every year. It is important for you to understand how machine-related hazards and unsafe actions around machines can put you at risk.
Machines can be unsafe in the following ways:
- Poor design. Machines that are poorly designed are inherently more likely to cause injuries than machines with a safer design.
- Inadequate maintenance. Machines that are poorly maintained can cause injuries because they don’t function properly.
- Improper installation. Machines that are not properly installed can malfunction and cause injury.
- Improper use. It is not safe to use a machine for a purpose for which it was not intended.
- Inadequate guarding. Machines that lack effective safeguards put workers at risk.
- Objects being discharged or expelled from a machine can injure the operator and other workers in the area.
Unsafe Actions
Unsafe actions around machines are also a major cause of injury. Examples of unsafe actions include:
- Reaching around, under, over, or through machine guards into hazardous areas;
- Removing or bypassing machine guards;
- Reaching into moving equipment in order to remove stuck or jammed material;
- Not using hazardous energy control procedures, or lockout/tagout, during service and maintenance;
- Wearing loose clothing, jewelry, or loose long hair around machines; and
- Not knowing how to properly maintain and repair machines.
To review some more machine safety basics, suggest students refer to the Handout Preventing Amputations.
Where Machine Hazards Occur
There are three basic areas of most machines that require safeguarding.
Point of operation
The point of operation is that point where work is performed on the material, such as cutting, shaping, boring, or forming of stock. The point of operation is typically the most hazardous part of the machine.
Power transmission apparatuses
Power transmission apparatuses are all components of the mechanical system that transmit energy to the part of the machine performing the work. These components include flywheels, pulleys, belts, connecting rods, couplings, cams, spindles, chains, cranks, and gears.
Operating controls
Operating controls or other moving parts are all parts of the machine that move while the machine is working. These can include reciprocating, rotating, and transverse moving parts, as well as feed mechanisms and auxiliary parts of the machine.
Knowledge Check 2
Now it’s time to see how much you’re learning about machine guarding.
Which of these can cause a machine to be hazardous? Choose all that apply.
- The machine operator is far away from the point of operation.
- The machine is not properly guarded.
- The machine is being used for a purpose it was not designed for.
- The machine is turned off and locked for maintenance.
- The machine has not been serviced recently.
― Improper guarding, using a machine for an unintended purpose, and failing to service and maintain a machine properly are all conditions that can increase the hazards of a machine.
Knowledge Check 2 (cont.)
What are the primary hazardous areas of a machine?
- Power transmission apparatus
- Point of operation
- Emergency stop
- Presence-sensing device
- Operating controls
― The power transmission apparatus, point of operation, and operating controls are parts of a machine that are likely to be hazardous. Emergency stops and presence-sensing devices are safety features, not hazards.
Knowledge Check 2 (cont.)
True or False. The power transmission apparatus of a machine is the point where work is performed on the material.
― False. The power transmission apparatus transmits energy to the point of the machine performing the work. The point where work is performed is known as the point of operation.
Point-of-Operation Hazards
Cutting:
Point-of-operation hazards cause thousands of injuries every year. Point of operation is the point where work is performed on the material.
- Examples include a drill bit or saw blade cutting into wood or metal
Punching:
Punching wood, metal, or plastic
Shearing.
Bending.
Compression:
The point of operation generally presents the highest hazard if you are a machine operator. The further away you are from the point of operation, the lower the hazard.
Power Transmission
The power transmission apparatuses of a machine are the mechanical parts that work with the power source to transmit energy to the part of the machine performing the work. Hazards of the power transmission apparatus include grabbing, nipping, or striking body parts or clothing.
Power transmission apparatuses include:
- Flywheels and pulleys
- Pulleys
- Connecting rods and couplings
- Belts
- Cams and cranks
- Spindles
- Gears and chains
Nip Points
Nip points are points on the machine where parts move toward each other or parts where a moving part moves past a stationary object.
Nip point hazards include having your hands, arms, or body caught, which can cause crushing, laceration, amputations, and even death.
Some examples of typical nip points are shown on this slide. Take a moment to examine them and think about where the nip points are on the machines you operate.
Operating Controls
Operating controls, or other moving parts, are all parts of the machine that move while the machine is working. These can include rotating, reciprocating, and transverse moving parts, as well as feed mechanisms and auxiliary parts of the machine. Some actions, such as cutting, may involve all of these motions.
Operating Controls: Rotating motions
Rotating motions can be dangerous; even smooth, slowly rotating shafts can grip hair and clothing, and through minor contact force your hand and arm into a dangerous position. Injuries because of contact with rotating parts can be severe. Collars, couplings, cams, clutches, flywheels, shaft ends, spindles, meshing gears, and horizontal or vertical shafting are some examples of common rotating mechanisms that may be hazardous. The danger increases when projections such as set screws, bolts, and keys are exposed on rotating parts.
Operating Controls: Reciprocating motions
Reciprocating motions may be hazardous because, during the back-and-forth or up-and-down motion, you may be struck by or caught between a moving and a stationary part. For example, you could be caught between a reciprocating table part and a wall.
Operating Controls: Transverse motions
Transverse motions, which are movements in a straight or continuous line, create hazards because you may be struck or caught in a pinch or shear point by the moving part. For example, you could catch a finger or hand in a machine belt.
Knowledge Check 3
Now, it’s once again time to see how much you’re learning about machine guarding.
Choose the best answers to these questions, select all that apply.
What is usually the most hazardous part of a machine?
- The operating controls
- A nip point
- A pinch point
- The point of operation
- The power transmission apparatus
―Usually, the point of operation is the most dangerous part of a machine.
Knowledge Check 3 (cont.)
Why can rotating machine motion be hazardous? Select all that apply.
- It can catch hair and clothing.
- It can cause electric shock.
- It can force your hands into a dangerous position.
- It can shut down the machine.
- It can cause dizziness.
―Rotating parts of a machinery can catch hair and clothing or force your hands and arms into a dangerous position, both of which can cause injury.
Knowledge Check 3 (cont.)
What is a nip point? Select all that apply.
- A place where machine parts move toward each other
- The place where an operator puts his or her hands
- The place where work is performed on material
- A part of the machine that protrudes from the main working area
- A place where a machine part moves past a stationary object
―A nip point is a place where machine points move past each other or a place where a machine part moves past a stationary object.
Purpose of Machine Guarding
The next slides will describe various kinds of safeguards designed to protect you from the machine injuries we’ve discussed. But first, it’s important to understand the fundamental purposes of machine safeguarding:
- Safeguarding prevents access to the point of operation and power transmission apparatus of a machine;
- Safeguarding keeps the operator out of the danger zones while a machine is operating; and
- Safeguarding prevents objects from being ejected from the machine toward you and other people.
Types of Machine Guards and Safety Devices
It’s important that you know the types of machine guards and safety devices in your workplace and why they are there. Types of machine guards include:
- Fixed guards or barriers between you and the machine’s power train or point of operation. Fixed guards generally provide the highest level of protection from machinery hazards.
- Interlocked guards, which automatically shut off the machine if opened or removed.
- Adjustable or self-adjusting guards, which can be moved to fit specific operations or accommodate material of different sizes.
Types of safety devices include:
- Presence-sensing devices—These cause a machine to stop if a body part gets too close.
- Restraints and pullback devices—These keep your hands and arms away from dangerous moving parts.
- Safety trip controls—These shut the machine down in an emergency. Examples include pressure-sensitive body bars and tripwire cables placed around the danger area that can be reached immediately by the machine operator.
- Two-handed control devices—These reduce hazards by requiring two hands to operate the machine, thus keeping you out of the danger zone.
Follow the “Safety Seven” Machine Guarding Rules
When you are operating or maintaining machines, always follow these basic “Safety Seven” rules:
- Don’t operate a machine that doesn’t have working guards. If a guard is missing or damaged, report it to your supervisor.
- Follow the AUTO rule—Never reach
- Around,
- Under,
- Through, or
- Over guards into hazardous areas.
- Never remove or bypass guards.
- Always shut down machines during service and maintenance. If you see a lock or tag on a machine, do not try to use it—that means it is being worked on.
- Never reach into operating equipment to remove stuck or jammed material.
- Always wear or use the appropriate protective equipment. For example, use push sticks or other feeding mechanisms, not hands and/or gloves, when feeding material into a machine.
- Clean and maintain machinery properly, replacing guards and making sure they are in place before using a machine.
Machine Guarding Best Practices
Being proactive regarding machine safety means taking steps while using your machine to avoid accidents before they happen. Here are some best practices to follow when it comes to machines and their safeguards.
- Never remove, disable, or try to bypass machine guards. And, only operate equipment when machine guards are in place and working properly. Do not use unauthorized or damaged machine guards.
- Don’t create new hazards, such as allowing objects to fall into moving parts or by creating a new pinch point.
- Lubricate the machine parts without removing the guard. If you can’t, turn the machine off.
- Immediately report any problems with machine guards to your supervisor.
- Check the machine manufacturer’s operating manual if you are unsure how to use a machine’s protective devices correctly.
- Never leave machines unattended with parts still moving. Remember that parts may still be moving after you have turned the machine off.
- Do not wear loose clothing, jewelry, or long hair around machines. These increase the risk of being caught in the machinery.
– Suggest to your class that for a review of these safety rules, they refer to the handout Machine Guarding Safety Checklist.
Knowledge Check 4
Now it’s time for one last quiz to see how much you have learned. Choose the best answer for each statement.
What is usually the most effective machine guarding method?
- Two-handed controls
- Presence-sensing devices
- Fixed guards
- Adjustable guards
- Interlocked guards
– In most cases, fixed guards provide the best protection from machinery hazards.
Knowledge Check 4 (cont.)
If you see a lock or tag on a piece of machinery, what should you do?
- Don’t use the machine.
- Try to remove the lock or tag.
- Try to start the machine.
- Remove the guards.
– If you see a lock or tag on a machine, do not use it; this means the machine is being repaired and should not be started. If you suspect that a lock or tag has been left on accidentally, contact your supervisor.
Knowledge Check 4 (cont.)
When is it safe to operate a machine without guards?
- When you’re lubricating the machine
- When the machine is working properly
- When someone is working on the machine
- Never
- When a guard is damaged or not working properly
– It is never safe to operate a machine without its guards in place.
Key Points To Remember
We’ve reached the end of this training presentation on machine guarding. This session gave you a good overview of the things you need to know to keep yourself safe when you work around machinery. The key points to remember about this training session are:
- Machine guards and safety devices are there to protect you.
- Never remove, disable, or bypass a machine guard or safety device.
- If you operate or maintain machinery, your exposure to unguarded or inadequately guarded machines can cause serious injury or death.
- Don’t operate a machine that doesn’t have working guards.
- And, if a guard is missing or damaged, report it to your supervisor