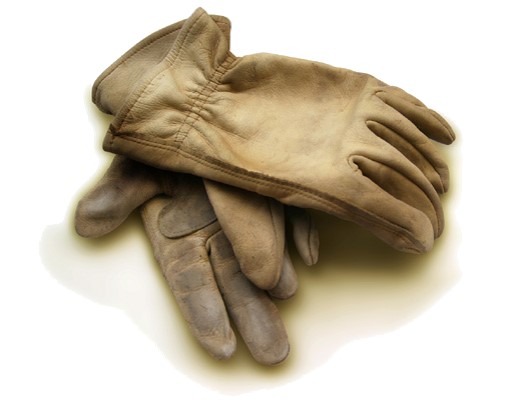
Nearly one-fourth of work injuries involve the hands and fingers. Your hands are used in just about every kind of work and therefore are vulnerable to many hazards. In this training session, we will look at the potential hand hazards in your workplace and the hand protection you are required to use on your job. We will also look at what can be done to prevent hand and finger injuries.
Table of Contents
Session Objective
By the end of the training session, you will be able to:
- Identify hand hazards;
- Choose appropriate gloves for work tasks;
- Know the limitations of hand protection; and
- Use and care for protective equipment.
Hands – Essential Tools
Hands and fingers are complex and versatile tools that we use for so many tasks that we often take them for granted. Think about how difficult it would be to do the different tasks listed on the slide if you had a broken finger, severely cut thumb, deep puncture in your palm, or other similar hand injury. Consider:
- Buttoning your shirt;
- Pouring a cup of coffee;
- Eating with a spoon or fork;
- Dialing and using the phone;
- Using hand tools; and
- Operating machinery.
Hands have the strength and flexibility to squeeze, grasp, and hold objects; the coordination necessary for playing the piano and typing; and the sensitivity for touching, feeling pressure and temperature, and performing delicate tasks. For all these reasons, do NOT take your hands for granted!
Hand Injuries
Here are hand injury statistics from the Occupational Safety and Health Administration, or OSHA:
- OSHA studies have found that nearly one-fourth of work injuries involve hands or fingers.
- OSHA also found that 70 percent of workers sustaining hand injuries were not wearing gloves.
- OSHA found that the other 30 percent were wearing improper or damaged gloves.
- We can probably conclude that if we were to wear the gloves, they were the proper gloves for the job and the gloves were in good condition, then we are not likely to sustain a hand injury. We will spend this training session determining the hand hazards and selecting the proper gloves for the job.
Hand Hazard Review
Let’s use this training session as an opportunity to review the potential hand hazards in our workplace. These are the primary types and causes of hand injuries. We will focus on each of the topics and the specific hazards associated with our workplace in the upcoming slides as follows:
- Skin absorption of harmful substances;
- Severe cuts or lacerations;
- Severe abrasions;
- Pinches and crushes;
- Punctures;
- Chemical burns; and
- Thermal burns
Skin Absorption of Harmful Substance
Our skin acts as an excellent barrier to many harmful substances. However, when our skin is broken these substances are more likely to penetrate this barrier and enter our bodies.
- Almost every type of solvent can be absorbed into the skin. Most solvents will only cause defatting, which results in dry and chapped hands. Some solvents may cause itching, rashes, or swelling. Other solvents can actually penetrate the skin and get directly into your bloodstream. These solvents can cause damage to internal organs.
- Exposure to harmful dusts causes skin irritation, which can result in dermatitis or skin rashes.
- Many of us have used pesticides, insecticides, or fertilizers at home. Many of these products are designed to penetrate the skin of animals or insects and kill them, so they can probably harm us as well. They may impact us after only one use or they may require years of use before we see symptoms of exposure.
Make sure you know what substances in your facility can harm your skin and hands.
Severe Cuts or Lacerations
You could receive severe cuts or lacerations on your hands when performing certain jobs as follows:
- Hydraulic or hand-operated presses can severely cut or crush a hand when it is placed in the point of operation. Guarding has been developed to prevent this from happening. This is why you must be properly trained before operating all equipment.
- Saws are a common tool in many workplaces. Obviously, with rotating blades, there is a significant hand hazard when using this type of equipment. Use tools, not your hands, to guide the material through the saws.
- Many hand tools involve the use of blades. Box knives, handsaws, skill saws, and circular saws could cause severe cuts if not used properly.
- Even straps or wires used in packaging boxes or bales can cause lacerations if handled improperly.
Make sure you know what machines and equipment in your facility could cause severe cuts and lacerations.
Severe Abrasions
Abrasions include mild skin scrapes, severe skin scrapes, tearing of the skin, and even removal of the skin (called de-gloving). Abrasions can happen when you are working with the following equipment:
- Sanders or grinders, with their rotating belts or wheels, could cause abrasions from minor scrapes to complete removal of the skin. This equipment must be properly guarded, and tools, instead of hands, should be used to guide the material into the sander or grinder.
- Conveyor belts have rotating belts that could snag your hand and cause severe abrasions. Belt and chain drives are similar to conveyors in that they could catch your hand in a pinch point and damage your skin.
- Rotating shafts (such as cams, flywheels, or spindles) can also snag your hand and mangle your skin or break bones.
- Finally, scrap metal or broken glass can cause severe abrasions or cuts if you were to handle this material with unprotected hands. Never sweep metal or glass pieces with your hands; always use a broom.
Make sure you know which equipment or machines in your facility could cause abrasions to your hands when improperly used.
Pinches and Crushers
- Pinches and crushes are probably the most common type of severe hand/finger injury. How many of you have ever smashed your thumb with a hammer? Probably almost everyone has at one time or another. However, gloves do not protect against pinching or crushing your hands.
- Machine guards protect your hands from getting into the point of operation, or the danger zone. Never disable or bypass a machine guard. Lock out all machinery before performing any type of maintenance.
- Material handling is a common way to pinch or crush your hand or fingers. Setting down or dropping a heavy object on your fingers or pinching your hand between a heavy object and the hand truck used to move it are common ways of injuring your hands.
- Finally, many people have smashed their fingers in a door.
Make sure you know which machines or operations in your facility can cause pinch or crush injuries when improperly used.
Punctures
Many tools and machines can cause punctures, including the following:
- A drill press can puncture right through your skin and muscle tissue. Punctures can be deep, which are more likely to result in infections. When using equipment that could cause punctures, stay focused on the task and keep your hands away from the point of operation.
- Nail guns can also cause punctures. This air tool, if handled improperly, could drive a nail all the way through your hand.
- Hand tools such as screwdrivers cause many punctures.
- And finally, even metal and wood slivers can cause deep punctures and infection. Always wear appropriate gloves when handling metal or wood pieces.
Make sure you know which equipment and operations can cause puncture wounds in your facility when improperly used.
Chemical Burns
Chemical burns can be very dangerous and are caused by several substances, including the following:
- Acids are used in many industries for a number of purposes such as metal etching and cleaning. Most acids will burn the surface of the skin and, depending on the concentration, may cause only mild discoloration of the skin or even severe third-degree burns. Some acids, however, will be absorbed into the skin and attack the bones or other tissue below the skin. Consult the acid’s container label and the safety data sheet, or SDS, for specific information about the acids in your workplace.
- Caustics are also used in many workplaces for water treatment, metal cleaning, or as part of chemical processes. Like acids, these will also burn the skin with a severity that depends on the concentration.
- Cleaning chemicals, especially those purchased for home use, are often corrosive and will burn the skin. Many bathroom and kitchen cleaners are caustic. Some tire and wheel cleaners are 60 percent to 70 percent acid. Read the labels to find out what protective gloves to wear.
Make sure you know which specific corrosive chemicals are used in your facility.
Thermal Burns
Thermal burns are another potential hand injury caused by the following jobs:
- Welding, cutting, and brazing operations have the potential for thermal burns. Wear appropriate gloves when performing this type of work.
- Steam operations have many opportunities for thermal burns. Boiler rooms have many hot tanks and pipes and steam pipes throughout the plant that could cause burns when touched. Any release of steam is an obvious hazard.
- Molten metal can reach thousands of degrees Fahrenheit and, therefore, requires many safety precautions because it can splash and cause severe burns.
- Finally, ovens used in industrial facilities for baking or drying can reach 400 to 500 degrees Fahrenheit and have many hot surfaces, including the outside surfaces of the oven.
Make sure you know the substances and processes in your facility that could cause thermal burns when improperly used and performed.
Cold and Frostbite
There are a number of workplaces and work environments where workers can be exposed to cold conditions.
- Construction workers are exposed to cold conditions in a number of work environments such as roof work in cold weather. Working on bridges near large bodies of water exposes workers to both the cold temperature and cold wind. Steel structures retain cold temperatures and quickly transfer the cold to the worker’s body. Working outside high-rise buildings can expose workers to cold temperatures and cold winds.
- Refrigerated rooms, containers, or vessels expose workers to controlled cold environments. These environments will typically not have a wind chill factor.
- Working with cold chemicals, such as liquid nitrogen or other liquid gases, can result in exposing your hands to the cold and potential frostbite.
- Commercial fishermen are exposed to cold weather, winds, and water.
- Finally, warehouses in colder climates are typically not heated in the winter so workers are exposed to cold temperatures.
Make sure you know the environments or processes in your facility that could expose you to cold conditions.
Other Hand Issues
Here are other hand hazards to be aware of:
- Carpal tunnel syndrome does not affect only office workers. It is caused when repetitive motions inflame tendons in the wrist and put pressure on the nerves. This results in numbness, weakness, and even pain in the hand, wrist, or elbow. Years of doing the same motion can eventually wear down the hand. Jobs and processes that could lead to carpal tunnel syndrome include mechanics always turning a wrench, carpenters always swinging a hammer, or data entry personnel always typing at the keyboard or using a computer mouse.
- Vibration can also damage the hands, causing numbness or other problems. Using hand tools that vibrate, such as drills, pneumatic socket drivers, hand sanders, or rivet guns, can damage the hands over long periods of use.
- Finally, fractures or compression, which often results in fractures, can occur when using almost any machine or hand tool. Material handling is also the cause of many fractures to the hands when objects are dropped on hands or the hands are smashed between the object and a door jam. Employees need to be aware of these potential hazards and understand how to avoid injury.
Make sure you know all the hand hazards in your facility.
Hand Hazards and Injuries – Any Questions?
- Now it’s time to ask yourself if you understand the information presented so far. Do you understand all the workplace hazards to your hands? It is important for your hand safety that you know what hazards to look out for.
Evaluate and Select Hand Protection
The OSHA standard (CFR 1910.138) states that these four items need to be considered when selecting hand protection:
- Consider the performance characteristics of the hand protection relative to the task to be performed. Determine if the task requires dexterity for delicate tasks, extra grip for slippery objects, or extra clean gloves so product is not contaminated.
- Consider the other conditions present. If you are handling sharp metal objects in an acid bath, gloves have to protect you from acid exposure. They also have to be cut resistant to protect you from the sharp objects and from acid exposure if the gloves’ integrity were compromised by the sharp objects. In addition, if the acid bath is heated, the gloves also have to protect the employee from thermal burns.
- Consider the length of time the gloves will be used. Chemical gloves are designed to protect against certain chemicals for a specific amount of time. If the employee is working 8 hours dipping parts into an acid bath and gloves are only rated for 4 hours of protection against that acid, the worker will have to get new gloves halfway through the shift.
- Finally, when selecting gloves, consider all the hazards as well as potential hazards that have been identified for each task.
Selecting Chemical–Resistant Gloves
Here’s what you need to consider when selecting chemical-resistant gloves:
- Consider the type of chemical. Acids, caustics, solvents, and oils have different requirements for gloves.
- Chemical contact considerations include the frequency and duration of contact, whether gloves are immersed in the chemical, and the chemical concentration. Usually, thicker glove materials will give better protection against higher frequency and duration of use and against higher chemical concentrations.
- Abrasion and cut resistance must be considered if there is potential for a puncture, cut, snag, or tear.
- The length and cuff type such as knit, wrist, or gauntlet, are important depending on whether you will immerse your hands only, your entire arms, or only use the material with a rag to wipe parts.
- Dexterity and grip must also be considered. If you are working with small, intricate parts and chemicals, gloves will have to be thin to provide better dexterity. If the chemical is oily, soapy, or otherwise slippery, the gloves may require extra grip.
- Finally, thermal protection may be required if you are dipping your hands into heated chemicals.
Chemical–Resistant Glove Materials
Chemical-resistant gloves are made from many different materials, because a single glove to protect against every type of chemical has not been invented. It is very important that you use the right glove material to protect against the chemical you are using. Here are the options:
- Butyl, a synthetic rubber, works well for a variety of chemicals, such as ketones, esters, alcohols, most inorganic acids, and caustics.
- Latex, or natural rubber, has good protective qualities against a variety of chemicals, including most acids and caustics, salts, detergents, and alcohols. However, many solvents will break latex down.
- Neoprene, a synthetic rubber with better properties than natural rubber, has good protective qualities against a variety of chemicals, such as oils, acids, caustics, and some solvents.
- Nitrile protects against a number of acids and caustics as well as some solvents and fuels.
Chemical–Resistant Glove Materials (cont.)
In addition:
- Polyvinyl chloride or PVC-coated gloves have good protection against some solvents, oil, and grease, as well as acids and caustics.
- Polyvinyl alcohol, or PVA, gloves protect against aromatics, ketones, and chlorinated solvents.
- Viton works well against aromatics, hydrocarbons, chlorinated solvents, ketones, acids, and amines.
- Finally, silver shield gloves resist permeation and breakthrough by more chemicals than any other material.
Make sure you know which chemical-resistant gloves to use for which operations in your facility.
Chemical–Resistant Glove Use and Care
Here’s how to use chemical-resistant gloves safely:
- Always inspect your gloves prior to using them. Look for cuts, tears, or punctures. Some gloves may become stiff or discolored after use. Dispose of gloves that are damaged or show signs of wear or chemical degradation.
- Avoid secondary chemical exposure by washing the outside of the gloves, before removing them, with soap and water and then rinsing with water.
- Carefully remove the gloves and avoid touching the outside of the gloves with your hands. One method to prevent contamination involves pulling the first glove off with the other gloved hand and then slipping ungloved fingers underneath the cuff of the second glove and removing it.
- Some gloves can be reused a number of times as long as the inside remains uncontaminated and they are inspected prior to each use. Some gloves will need to be discarded because the chemical they contacted may permeate the material and reach inside the glove in such a way that the inside is contaminated.
- Finally, place gloves intended for reuse in a dry and clean area. Hang the gloves in such a way that they will dry out.
Selecting Cut, Abrasion, & Puncture-Resistant Gloves
Here’s what to consider when selecting cut-, abrasion-, and puncture-resistant gloves:
- Common cut-resistant gloves include: metal mesh, which is made of stainless steel rings, steel core, which is a fabric with steel woven into the material, Kevlar®, which is what bulletproof vests are made of, or rubber-coated fabrics. Your choice will primarily depend on the level of cut resistance needed. A person using a box knife will not need the same protection as someone using a sharp knife to fillet fresh fish.
- Consider the length and cuff requirements. If forearm protection is needed, you will require a longer glove.
- Dexterity and grip. Meat cutters will need to be able to grip slippery materials and have the dexterity to handle a knife.
- Finally, thermal protection may be required when handling hot or cold steel parts that have rough, sharp edges.
Make sure you know which cut-, abrasion-, or punctureproof gloves to use for which jobs in your facility.
Selecting Disposable Gloves
Here’s what to consider when selecting disposable gloves:
- Although there are other types of gloves that are considered “disposable,” the term usually refers to thin-walled latex and nitrile gloves used in the healthcare sector. These gloves protect workers from bloodborne pathogens and germs.
- Until recently, the most common form of disposable glove was made of latex. Many people are discovering they are allergic or sensitive to latex and cannot wear latex gloves.
- Nitrile gloves have proved to be comparable to latex. They provide similar protection, dexterity, and feel, and often have better tear strength than latex gloves.
- Latex and nitrile gloves also provide protection from some chemicals at low concentrations and short durations.
- These disposable gloves rip, tear, and puncture easily. Some tasks may require putting on two layers of gloves in case the outside layer tears or rips in the middle of the task.
- Finally, the size of disposable gloves is important. The gloves will tear when putting them on if they are too small and they will be a hazard if they are too large and loose on your hands.
Make sure you know which jobs in your facility require the use of disposable gloves.
Selecting Electrically Insulated Gloves
Here’s what you need to know about using electrically insulated gloves:
- Electrically insulated gloves are designed for workers that handle live wires or energized electrical equipment. They protect workers from the dangers of high voltage lines and equipment.
- Electrically insulated gloves must be tested every 6 months to check the integrity of the glove.
- If a pair of gloves has not been tested in the past 12 months, the gloves cannot be used and should be segregated and marked “Do Not Use.”
- Finally, before putting on electrically insulated gloves, it is very important that you inspect them for any obvious signs of wear or holes.
Selecting Other Gloves
Other tasks require other types of specialized gloves.
- Welders’ gloves and aluminized gloves work for very hot temperatures.
- Insulated neoprene gloves or freezer gloves should be worn for working with cold chemicals or in cold environments.
- Antivibration gloves are designed to reduce the transfer of vibration from a powered hand tool to your hand. These gloves usually contain some sort of padding, which protects your hand from the vibration.
- Finally, general work gloves, typically made from leather, will protect against wood and metal slivers, abrasions from working with rocks or ropes, or general cuts and scrapes when working around the house.
Make sure you know which types of gloves to use for which jobs in your facility.
Gloves Selection – Any Questions?
- Now it’s time to ask yourself if you understand the information presented so far. Do you understand how to select and use the right gloves for the job? It is important for your hand protection that you use the right glove in the right way for the job you are performing.
General Glove Use and Care
Always follow these general glove use and care instructions:
- Make sure the gloves fit your hand properly. Gloves that are too small will limit your hand’s mobility and could tear. Gloves that are too big will limit your dexterity.
- Hands should be clean before using gloves. If you put dirty or greasy hands inside your gloves, you are subjecting your hands to potential irritation because dirt and chemicals are being rubbed into your skin inside the glove.
- Fabric and leather gloves should be cleaned regularly or discarded.
- Inspect gloves for damage before wearing them. Replace gloves if they have tears, holes, or other minor defects.
- Make sure gloves are the right length for the job.
- Finally, do not use fabric or leather gloves on liquid chemicals because the material will soak up the chemical.
Make sure you follow your facility’s glove use and care instructions.
Contaminated Glove Removal
If your gloves are heavily contaminated, if you handled extremely toxic chemicals, or if you were not able to clean the gloves, it is important that you know how to remove them safely. In addition to the method described on this slide, other methods include using inner gloves or asking another employee to remove them.
- The goal is to prevent your bare hands from touching the outside, contaminated, surface of your gloves.
- Grasp the outside of the glove near the cuff on one of your hands with the other gloved hand. Pull the glove off.
- Now insert fingers from the hand without a glove under the cuff of the glove on your other hand.
- Begin to pull the glove off, then grasp the inside (clean) surface of the glove and pull it off your other hand.
Glove Limitations
Here are the jobs or locations where you should not wear gloves because it is unsafe to wear them:
- Gloves can get caught in moving machinery, such as powered rollers, belts, pulleys, chain drives, and rotating or moving parts such as motor shafts.
- Some people are allergic to latex gloves so it is important that other gloves, such as those made of nitrile, are provided.
- Gloves can actually cause more problems if chemicals get inside them.
- Finally, gloves can fail in conditions of extreme temperatures, high mechanical force, high vibration, or when handling extremely harsh chemicals.
Make sure you know the jobs and locations in your facility where you should not wear gloves.
Prevent Dermatitis
Here’s how to protect your hands from dermatitis caused by wearing gloves:
- Always wash your hands after removing gloves, especially after working with a chemical.
- Use skin moisturizers to replace natural oils and prevent dryness and cracking.
- Finally, use barrier creams to protect against mild chemicals that could potentially irritate your skin and cause rashes.
Glove Protection – Any Questions?
- Now it’s time to ask yourself if you understand the information presented so far. Do you know how to use and care for gloves? It is important for the safety of your hands that you know how to use gloves to protect them.
Key Points to Remember
Here are the key points to remember from this training session on PPE for your hands:
- Know the potential hand hazards in your workplace.
- Understand the types of gloves needed to protect against chemicals in your workplace.
- Wear cut-resistant gloves when using knives or working with sharp objects.
- Keep hands out of a machine’s danger zone.
- Finally, do not wear gloves around machinery with moving parts.
This concludes this training session.