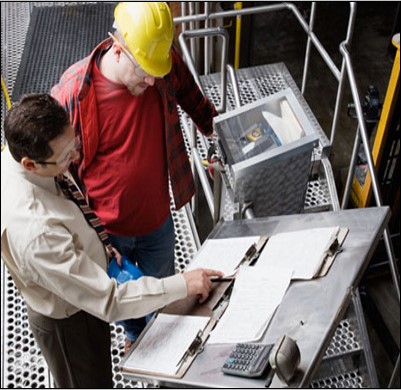
Although you’re not employed by our organization, you are still expected to follow the same safety rules as our employees when working in our facility. These rules are designed to prevent accidents and ensure the health and safety of everyone working here—employees and contractors alike.
In today’s training session we’ll review the key elements of our safety program and place special emphasis on any safety rules that are specific to our facility. We won’t have time to cover every single safety hazard, however, so once you’re on the job you may have some questions. If you ever have any questions about any potential hazard or other safety issue, please ask one of our supervisors immediately. Your safety is important to us, and we want to do everything we can to make sure you keep safe and avoid injuries while working here.
Table of Contents
Session Objectives
The main objective of this session is to make sure you understand our safety rules and policies so that you can avoid accidents and injuries while you are in our facility. By the time this session is over, you will be able to:
- Recognize the hazards of our workplace;
- Understand emergency procedures and accident-reporting rules;
- Follow safety policies and safe work practices; and
- Avoid accidents and injuries in our facility.
Evacuation
The first thing you need to know about our safety program is our emergency procedures.
- Listen for the alarm and instructions telling you to evacuate.
- Follow the nearest escape route. Move quickly but calmly. Your escape route could include going down halls, aisles, past equipment, and so on. Learn the various escape routes from the area you’ll be working in. If, during an emergency, you can’t remember the evacuation routes, follow our employees or ask for assistance.
- Exit the building through one of the many exit doors.
- Once outside, proceed immediately to your assigned assembly area. Don’t leave the assembly area until instructed to do so.
- We’ll conduct a head count of employees and contractors to make sure everyone has safely evacuated. Don’t return to the building until the all clear has been given.
Are you familiar with our evacuation procedures? You should be.
Chemical Spills
If there is a chemical spill or release while you’re working here, it’s very important that you know what to do.
- First and most important, never attempt to stop the spill or leak. Don’t try to contain or clean up the spill. The only personnel allowed to respond to chemical spills are employees or contractors who are specifically trained and equipped to respond to a release of hazardous chemicals.
- If you see or smell a chemical spill, immediately warn others who are working in the area near you.
- Turn off any ignition sources. Also turn off any equipment that could ignite a flammable chemical.
- Evacuate the immediate area near the spill and follow instructions from our safety personnel. You might be required to evacuate the building or you might be asked to move to a different part of the facility temporarily.
- Help keep other contractors and employees out of the area until it has been cleaned up by a special response team.
Think about what you need to do in the event of a chemical spill so that you will be able to act quickly and effectively in case of emergency.
Accidents or Injuries
- You must report all accidents or injuries that occur while working in our facility, even if no one is injured.
- If someone is injured and is bleeding, do not touch the blood with bare hands. Universal precautions are required to protect against potential bloodborne pathogens. This means treat anyone’s blood as if it is infected, even if you don’t think it is. Wear disposable gloves from the first-aid kit or have the person put pressure on the wound himself or herself.
- First-aid kits are available throughout the facility. After going to your designated work location, find out where the nearest kit is located.
- If someone is badly injured and needs emergency medical attention, call 911 before you start first aid, or ask another worker to make the call while you begin first aid.
- All accidents will be investigated to determine causes and to implement steps to prevent the accident from happening again. We’re not interested in assigning blame. We’re interested in preventing accidents.
- Don’t clean up an area where an accident has occurred until after our people have had a chance to look at the scene so that we can figure out what happened.
Do you know the steps you need to take to report an accident or injury?
Emergency Equipment Must Be Accessible
Emergency equipment must always be accessible. You may bring equipment, tools, carts, materials, or even vehicles into the facility in order to do your work. Make sure these items do not block emergency equipment. If you’re not sure where to place your materials or equipment, ask an employee or one of our supervisors.
- Access to exit routes and doors must always be clear. Do not temporarily store tools, carts, materials, or equipment in exit routes.
- Don’t block fire extinguishers either. They must be easily accessible.
- Electrical panels need 30 inches of clearance at all times, just in case the power needs to be shut off in an emergency.
- Paths to emergency showers and eyewash stations must also be clear. And first-aid stations must be accessible and visible to all.
- Chemical spill response materials must always be accessible to the response team as well.
When you get to your designated work area, be sure to look for emergency equipment and take steps to make sure it’s kept clear.
Policies
We work hard to maintain a drug-free workplace in order to protect the safety of our employees and contractors like you. We select contracting companies that have similar policies.
- Drugs and drug use are forbidden in our workplace, as is coming to work under the influence of drugs.
- We also expect contractors to not be under the influence of alcohol or to not bring alcohol to work. Do not drink before or during work.
- We will test employees and contractors for drugs if we have reasonable suspicion, such as strange behavior or the smell of alcohol on a person’s breath.
- Weapons such as guns and hunting knives are not permitted on the property of this facility either.
- In addition, we require all those who enter our facility to obey all safety signs, such as signs requiring the use of special personal protective equipment, or PPE.
Are you familiar with our drug and alcohol policy and testing procedures? You should be. If you need more information, speak to one of our supervisors.
Restricted Areas
You may be given access only to the specific area in which you are assigned to work, or you may have more freedom of movement through the facility. However, you should know that there are some areas that are restricted, and only authorized personnel are allowed to enter. For example:
- Confined spaces are restricted to trained entrants and only when given permission with a confined space entry permit.
- Chemical storage areas are generally restricted to personnel who work with those chemicals.
- Specific chemical processes may also be off limits.
- Laboratories in which chemicals are handled or quality control testing is conducted are also typically restricted to authorized personnel.
- There may be other areas, such as high-noise areas, where you are not permitted unless your work requires it.
- You may also need to set up restricted areas to keep our employees out of operations you’re performing that could be hazardous.
Make sure you obey signs restricting entry to parts of the facility.
Job Safety Assessments
A job safety assessment, or JSA, is a way to evaluate specific jobs or tasks, identify hazards, and then describe how to safely perform that job in a way that avoids injury.
- As a contractor, you will be required to review the JSA for the job that you will be assigned to perform.
- The first column of a JSA describes the job steps. This column tells you how to perform the job, what steps to take, and the proper sequence of steps.
- The second, or middle, column describes the potential hazards of each job step. Hazards might include sharp objects, chemical hazards, falling objects, electrical hazards, and so on.
- The third column describes how you can avoid being injured by the hazards described in the second column. This might include wearing PPE, using a lifting or material-handling device, and so forth. This third column essentially lists the safe work practices required for the job.
Think about the job you will be performing here. Do you know the steps, the hazards, and the required safe work practices?
PPE
Our organization has conducted PPE hazard assessments for the jobs that are typically performed in our facility and selected PPE specific to each job or task. You will be expected to wear the same PPE that our employees wear. But if you are here to do specialized work, such as confined space entry, machine repair, or construction, you and your employer will need to conduct a PPE hazard assessment with us so that together we can select appropriate PPE for your specific tasks. Generally speaking, however, the following types of PPE might be required, depending on the job you are performing:
- Eye protection in the form of safety glasses may be required to protect your eyes from impact hazards or goggles might be required to protect against dust or chemicals.
- Face shields might be necessary to protect your face from impact, chemical splashes, and so on.
- Protective clothing might be required to protect against chemical hazards, heat, electrical hazards, welding hazards, and so forth.
- Gloves are frequently needed to protect hands from chemicals, splinters, cuts and bruises, heat, electricity, and other hand hazards.
- Respirators may be necessary to protect you from breathing hazardous vapors, mists, fumes, or dust.
- And if you are assigned to work in a noisy area, you will be required to wear hearing protection such as earplugs or earmuffs.
- Special safety footwear may be required to protect your feet from falling objects, punctures, chemicals, heat, and other hazards.
Think about the PPE you are required to wear on the job. Do you know how to select the right protection and use it properly?
Safely Handling Materials
If you will be working with or near hazardous materials, you need to understand the hazards and know the precautions you must take.
- Safety data sheets, or SDSs, contain valuable safety and health information about the chemicals in our facility. Do not work with a chemical unless you have reviewed the SDS.
- Container labels also provide much useful information about hazards and precautions. Always read the label as well as the SDS.
- You need to know where materials are located in the facility and stay out of these areas unless you are authorized to be there.
- We store materials in special ways to prevent fires and chemical releases. Do not move or transfer chemicals unless you have received specific training on how to handle and store the chemicals. If you handle any chemicals on the job, you must be familiar with the hazards and precautions. Do you know where to find SDSs and how to use them to protect your safety and health?
Lockout/Tagout
If your job involves repairing machinery or working in a confined space, you will be required to lock out equipment to do your job safely.
- Before performing lockout, you must identify all potential sources of energy that require lockout/tagout. Hazardous energy includes electrical, hydraulic, pneumatic, mechanical, gravity, and so on.
- We have developed machine-specific procedures for conducting lockout/tagout for every machine in our workplace. You should review and follow these procedures.
- You are required to use locks and tags that meet OSHA requirements.
- If a group of people are working in a lockout situation, each person must place a lock on every lockout point. A person in charge will be designated to ensure that all lockout procedures are followed.
- After applying locks and before beginning work, test the equipment to make sure all hazardous energy has been controlled.
Think about the required lockout/tagout procedures you will be required to use in our facility. If you have any questions, speak to the supervisor in charge of the lockout.
Confined Spaces
- If your job involves entering a confined space, you must first review our written confined space entry program and familiarize yourself with required procedures.
- An entry permit must be issued before you are allowed to enter the space. The permit ensures that required safety precautions have been taken and the space is safe to enter.
- All entrants must understand potential hazards of the confined space, including any atmospheric or mechanical hazards as well as engulfment or entrapment hazards.
- In addition, rescue equipment must be available and ready to use. Trained confined space rescuers must be notified and available as well.
- Entrants and attendants must follow all the rules listed on the permit. They must also be in constant communication with each other and be prepared to get the entrants out safely in an emergency.
Think about the safety precautions required when entering confined spaces. Make sure you understand and follow the provisions of our OSHA-required confined space entry program.
Basic Safety Rules: True or False?
Now let’s take a little true/false quiz to test your knowledge of the basic safety rules we’ve just discussed.
- You should learn various evacuation routes from where you’re working. True or false? The correct answer is “True.” One route could be impassable because of fire or smoke.
- Only report accidents with injuries. True or false? The correct answer is “False.” Report all accidents.
- Drugs, alcohol, and weapons are not allowed in our workplace. True or false? The correct answer is “True.” You are not allowed to come to work under the influence either. We will use drug testing to enforce the policy.
- As a contractor, you do not have to review job safety assessments. True or false? The correct answer is “False.” You should always review available job safety assessments to learn about hazards and precautions.
How did you do? Did you get all the answers right?
Basic Safety Rules
Now it’s time to ask yourself if you understand the information presented so far.
- Do you understand what we’ve discussed about emergency response?
- About reporting accidents and injuries?
- About our policies and restricted areas?
- About job safety assessments and PPE?
- And about special safety concerns such as chemicals, confined spaces, and lockout/tagout?
You need to understand all of this information in order to keep safe on the job. Now let’s continue to the next slide and talk about machine safety.
Machine Safety
Machine safety rules you need to remember are:
- Don’t touch any machines or process equipment in our facility unless you are trained and certified by us that you are qualified to operate the equipment.
- If you are authorized to operate any of our equipment, you will be trained by our personnel about the operating steps, the hazards, and the safe work practices you need to follow to operate the machines safely.
- Be sure to inspect any machine you use before each use. Make sure all guards are in place and that emergency stop devices and warning lights are working properly.
- Also be sure to immediately report any machine malfunctions. Do not operate a machine if guards are not working properly or if there is any other problem with the equipment. Do not attempt to repair a malfunctioning machine yourself. Just report it, and leave the repairs to our personnel.
Heavy Equipment
In some cases, you may need to bring heavy equipment into our workplace to perform your job.
- Equipment such as forklifts, scissor lifts, personal lifts, backhoes, tractors, or trucks may be necessary.
- If you operate any such equipment on our property, you must have a current training certificate and be proficient in the operation of that equipment.
- You are required to inspect your equipment each day before use to ensure that it is safe to use.
- While operating the equipment, you must watch for pedestrians and follow our traffic rules. We may also ask you to take part in training our workers to safely work near your heavy equipment.
Working at Heights
If you have to work at heights while you’re here, we want you to be sure to take proper precautions to prevent falls.
- Always use ladders safely. Inspect them before use. Set them up on a firm base. Angle extension ladders out 1 foot for every 4 feet of height. Have someone hold the ladder for you. Tie off the top, if possible. And don’t stand on the top three rungs of an extension ladder or the top two steps of a stepladder.
- Erect scaffolds correctly and inspect them daily. Make sure platforms, guardrails, and toe boards are properly installed.
- We have guardrails along any aboveground work platform or walkway. Report any problems with guardrails right way.
- If your work requires you to be outside an area with a guardrail, you are required to wear personal fall protection equipment with a harness, lanyard, and engineered anchor point. Be sure to inspect this equipment carefully before each use. Also remember that using personal fall protection equipment requires special training. If you have not had this training, do not attempt to use this equipment or perform a job that requires the use of this equipment.
Electrical Safety
We are also concerned about your safety if you are working near electrical systems. If you are not specially trained to work with electricity, you are considered “unqualified” by OSHA.
- This means you must stay away from electrical components— especially exposed live electrical parts. Do not open electrical panels or attempt to fix electrical conduits or malfunctioning equipment if you are unqualified.
- Only trained and “qualified” workers are permitted to work with exposed live electrical parts, install electrical components, and repair electrical equipment.
- If you are qualified and authorized, wear proper PPE whenever you work with electrical components. This includes gloves, boots, protective clothing, and a nonconductive hard hat. And use tools that are designed to withstand the voltage you will be working with.
- If you are qualified to repair electrical equipment, be sure to follow our lockout/tagout rules and de-energize and lock out equipment before working on it.
Welding and Cutting
- All welding and torch-cutting operations in our facility require a hot-work permit. A hot-work permit is basically a checklist to ensure that flammable and combustible materials are cleared at least 35 feet from the welding area and that all other necessary precautions are taken to prevent fires.
- We require you to install a welding screen around the work area to protect the eyes of other people working nearby.
- A fire watch must be maintained during and after welding and cutting operations.
- Compressed gases must be used safely. They should be stored upright with caps on when the cylinder is not in use. And they should be adequately secured when stored so that they cannot be knocked over.
Lift Safely
Back injuries are among the most common workplace injuries. Here are some basic rules to help prevent back injuries.
- Before manually lifting or carrying heavy items, consider using material-handling aids such as pallet jacks, hand trucks, carts, or hoists.
- When you must lift heavy, awkward items, get a partner and lift the object as a team.
- When lifting any object, make sure you have a solid base. You should have your balance with feet spread shoulder-width apart. Do not stand on a slippery surface.
- Squat down over the object. Make sure your back is straight. Grasp the object with a firm grip.
- Lift straight up with your leg muscles, not your back muscles.
Think about how you normally lift heavy objects. Do you follow these rules?
Housekeeping
Housekeeping is very important to prevent accidents—especially those caused by slip and trip hazards. Our employees work hard to maintain work areas in a clean and safe condition. We ask you to do the same.
- If you spill liquids such as coffee or water, please clean them up right away. Failure to do so could mean that the next person who comes along slips and falls.
- Pick up plastic, trash, or other materials that could cause someone to slip and fall. Even if you didn’t drop the item, pick it up and dispose of it properly.
- Also put away tools and materials so that they do not become a tripping hazard.
- When you have to stretch out electrical cords or air hoses, watch where you lay them. Try to keep them out of aisles and walkways.
- If they must be laid across a walkway, tape them down as much as possible to reduce the trip hazard.
Do you always make an effort to keep the areas in which you work safe and free of housekeeping hazards? We expect you to do so here.
Good Hygiene Practices
We also expect you to follow good hygiene practices to stay healthy on the job.
- Do not eat, drink, or bring food and beverages into work areas— especially when working with or near chemicals. Keep food and beverages stored in an appropriate place, such as the break room, and consume it there as well.
- No smoking is allowed in the workplace. Smoke only in designated smoking areas outside the building.
- Wash hands before going on breaks to eat, drink, or smoke. You don’t want to contaminate food or drink with chemicals, dirt, or grime from the workplace.
- If your clothes become contaminated with hazardous chemicals, remove them. Do not wear them all day at work, and do not wear them home. Wash contaminated clothing separately from other laundry.
Do you know the designated smoking areas at our facility? Remember, you are only allowed to smoke in those places.
Safety Procedures: True or False
Now let’s review the safety procedures we’ve just discussed with a short test. Look at the statements on the screen and decide which ones are true.
Ready?
- Lift with your back muscles. False. Lift with your legs.
- Use any machine you know how to operate. False. You should only use our equipment if you are trained and certified by us.
- Don’t try to fix electrical equipment or do other electrical work unless “qualified.” True. “Qualified” means trained and authorized according to OSHA regulations.
- If you didn’t drop it or spill it, you don’t have to clean it up. False. Good housekeeping rules require everyone to do their part to keep the work area safe.
- Smoking is permitted only in designated areas. True. Smoking is not allowed anywhere else, under any circumstances.
How did you do? Did you get all the answers right?
Contractor Safety Procedures
- Do you understand all the safety procedures and practices that we’ve discussed in the previous slides?
This information is very important. Your health and safety on the job depend on your knowledge of this information. Now let’s conclude the session with a reminder about hazard awareness, followed by key points to remember from this training session.
Hazard Awareness
- To prevent accidents and injuries on the job, it’s especially important as a contractor in an unfamiliar work area to plan each job carefully before starting work so that you can anticipate and control any potential hazards. Never just jump into a task without thinking about what could go wrong.
- Consider all the potential hazards. Review the job safety assessment if one is available for the job you’re doing. If not, make your own assessment. Talk to our supervisors and ask questions to become more familiar with the potential hazards in the area where you’ll be working.
- Inspect tools and equipment to make sure they are all in good, safe condition.
- Never take any shortcuts. Follow all safe work practices. And work at a safe, steady pace. Don’t rush.
- If you’re unsure about any hazard or precaution, ask questions. Never start a job until you are completely sure you know all there is to know about how to perform it safely.
Key Points to Remember
Here are the main points to remember from this session on contractor employee safety:
- Know how to respond to emergencies;
- Follow our policies;
- Pay attention to warning signs;
- Review job safety assessments and make hazard awareness a priority;
- Read safety data sheets, labels, and other written safety instructions; and
- Follow all OSHA requirements.
This concludes the Contractor Safety training session.