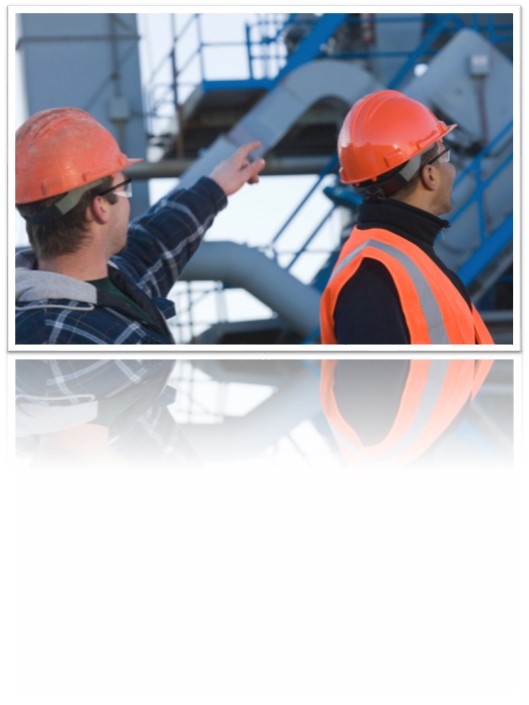
Today we’re going to talk about job hazard analysis. Job hazard analysis, or JHA as it’s often called, is an essential part of our safety program. Through JHA, we are able to identify workplace hazards and risks, and control, reduce, or eliminate them. All employees need to understand and participate in JHA in order for us to be successful in preventing accidents, injuries, and work-related illness.
Table of Contents
Session Objectives
The main objective of this session is to make you more familiar with job hazard analysis. By the time this session is over, you should be able to:
- Identify the purpose of JHA;
- Recognize the benefits of JHA;
- Understand the JHA process; and
- Analyze jobs effectively to detect and correct hazards.
Prequiz: Test Your Knowledge
Before we begin, let’s take a short prequiz to see how much you already know about job hazard analysis.
- See if you can answer these three questions correctly: Here are the answers.
How did you do? If you got them correct—congratulations, you are well on your way to learning about job hazard analysis! If you didn’t get all of them correct, don’t worry. We will be going over this information and much more during this session.
Regulatory Guidance
- Although OSHA has no specific job hazard analysis standard, many OSHA standards require employers to conduct workplace hazard assessments so that proper precautions can be taken to protect you and your coworkers. One example is the PPE standard, which requires a hazard assessment to determine what type of PPE is required.
- To help organizations conduct effective hazard assessments, OSHA has developed guidelines on job hazard analysis. The guidelines themselves are not regulations or requirements; however, following them helps companies comply with OSHA standards generally, in addition to preventing workplace accidents, injuries, and illnesses.
- And even though OSHA doesn’t require JHA, if we were ever inspected by OSHA, the inspector would very likely want to see our hazard assessment program. So we want to be sure we analyze job hazards accurately and frequently throughout our facility.
- One final introductory point. Throughout this session, we’re going to use the term job hazard analysis, or JHA for short. But you may have also heard this type of hazard analysis referred to as job safety analysis, or JSA. Both terms refer to basically the same process.
What Is JHA?
What is job hazard analysis?
- It is a method of identifying the risks and hazards associated with each job we perform. If we don’t identify all of them, we can’t take corrective action to prevent accidents and injuries. So JHA is really essential to your safety and health on the job.
- JHA also helps us break jobs down into simple individual steps, allowing us to pinpoint all the risks and hazards associated with each step. If you look at an operation as a whole, you might see five or six risks or hazards. But when you break the operation down into simple discrete steps, you might realize that there are five or six risks or hazards associated with each step in the operation.
- As you can already see, JHA provides a system for easily understanding job hazards or risks. So it’s very important for you to understand what job hazard analysis is and how it works. And that’s what this training session is all about. So please pay careful attention.
Why Perform JHA?
Why perform job hazard analysis? Well, we’ve already partly answered that question. But let’s look more closely.
- JHA not only helps us identify existing hazards or risks associated with each step in a job, but
- It also helps us identify potential hazards or risks. Some are virtually invisible until you break the job down into simple discrete steps and examine each individual step in the operation.
- JHA also helps us prioritize corrective actions. It tells us where to focus our time, energy, and resources so that we can deal with the most serious hazards first, the ones that can cause the most severe injuries or present the greatest risk of serious health problems. Not that all hazards and risks aren’t important. But we need an organized, prioritized way of going about dealing with workplace hazards.
- When JHA is properly conducted, we are able to reduce, control, or eliminate workplace hazards or risks. And that’s the real answer to the question, Why perform JHA? Because if we reduce or eliminate hazards, we reduce or eliminate the risk of accidents, injuries, and job-related illness.
Are you familiar with our JHA policy and the reasons we perform JHA in our facility? Everyone should be.
What Are the Benefits of JHA?
JHA has many benefits for you and for the organization as a whole.
- The main benefit, of course, is that JHA reduces accidents, injuries, and illness, thereby improving safety performance.
- Because JHA reduces injuries and illness, it also reduces absences. This means we have more fully qualified people on the job every day, which means you don’t have to do extra work to cover for sick or injured coworkers. And it also means that each one of us is safer on the job. When we’re fully staffed, people aren’t stressed or overburdened, which means they can take their time and work safely.
- More people at work every day means increased productivity as well. It means we’re able to meet production schedules and keep our organization operating at peak performance.
- JHA also helps improve workplace morale. When people feel safe in the workplace, they’re happier and more satisfied with their jobs. And that means we can all do our best and contribute to the success of the organization.
- Another very important aspect of JHA is that it helps us comply with OSHA and similar workplace regulations. When we know about all the hazards, we can take the necessary steps to protect everyone as the regulations require.
How Are Jobs Selected for JHA?
Our next question is, How are jobs selected for JHA? That’s an important question because, as we said earlier, for JHA to be effective, we have to prioritize. We can’t analyze all jobs at once. So,
- We start with jobs with high accident, injury, or illness rates. Obviously, those are the jobs with the most serious safety and health risks, and we need to address those problems first.
- Also high on the list for JHA are jobs where there have been a lot of near misses. Maybe nobody has been hurt so far, but these are accidents waiting to happen, and we want to correct the problem before somebody does get hurt.
- Jobs with procedure, process, or equipment changes are also high-priority targets for JHA. Any of these changes can result in new, unanticipated hazards or risks. Or they may reduce, control, or eliminate them. Either way, we need to know.
- After we’ve analyzed the jobs where accidents are most likely to occur, we work our way down through less hazardous jobs until we’ve made sure that through JHA, we’ve come to understand all the hazards and risks associated with every job in the workplace.
Of course, since things are always changing, the job is never done. JHA is an ongoing process.
Who Is Involved In JHA?
To be successful, JHA must be a total team effort that involves nearly everyone in the workplace. Generally speaking, the following people are involved in each job hazard analysis we conduct:
- Safety personnel who are trained to identify hazards and know regulatory requirements;
- Department managers and supervisors who know production processes and schedules and have the authority to implement changes;
- Employees who perform the jobs and know them so well;
- Design engineers who design the operation and help “design out” identified hazards; and
- Maintenance personnel who work on our equipment and are familiar with potential failure or risk scenarios in our work areas.
If you’ve been involved in a JHA, you may remember all the different people who participated. Think about the information you have about your job that you can contribute to the next JHA.
How Are Hazards Identified?
The next question we need to ask about job hazard analysis is, How are hazards and risks identified? There are several different ways.
- General inspections can be performed by a number of different people. But most often they are conducted by safety professionals who are familiar with workplace hazards and risks and understand the regulatory requirements. General inspections usually involve a review of the entire facility from wall to wall. They are very comprehensive and also very time-consuming.
- Special inspections focus on areas where safety and health concerns or risks have been discovered. Special inspections are targeted, and investigate only certain operations. Safety personnel along with managers, supervisors, and employees involved in these operations usually work together to conduct special inspections. We might even call in outside experts to help us.
- Walkaround inspections are usually conducted within a department on a routine basis—daily, weekly, or monthly. Supervisors are generally responsible for these inspections or the work areas they supervise. They report any possible concerns they find to safety personnel.
What Are OSHA’s Inspections Guidelines?
OSHA offers us guidance through its JHA guidelines about what, when, and how to inspect the workplace and document our findings. For example, OSHA JHA guidelines recommend:
- Listing departments and operations involved in different kinds of workplace safety inspections;
- Listing and describing operational activities in areas being inspected;
- Assigning inspection dates and duties;
- Determining the sequence of inspection activities and the route of the inspection; and
- Identifying and describing follow-up responsibilities resulting from inspections.
What’s the Function of Area Hazard Checklists?
To assist in inspections and to facilitate the identification of workplace hazards we use area hazard checklists. These checklists help us evaluate:
- Equipment
- Procedures
- Personnel
Are you familiar with the area hazard checklists we use in job hazard analysis? If not, ask your supervisor or the safety director if you can see the checklist for your work area.
Which Elements of a Job Are Analyzed?
During JHA inspections the people conducting the inspection will be looking closely at all the discrete elements involved in an operation or process from start to finish. In other words, they’ll be watching the following actions closely:
- Start-up;
- Activities that take place during the operation or process;
- Shutdown; and
- Maintenance.
All of the elements must be analyzed because there may be—and usually are—hazards and risks associated with all of them.
JHA Explained: True or False?
Let’s do a knowledge check on what you’ve learned so far. Decide whether the statements on the screen are True or False. Let’s begin.
- JHA looks at the workplace as a whole. True or False?
- We perform JHA because OSHA’s JHA standard requires it. True or False?
- Routine safety inspections provide valuable information for JHA. True or False?
- And finally, only safety personnel are involved in JHA. True or False?
How did you do? Did you get all the answers right?
JHA Explained
Now it’s time to ask yourself if you understand all the information about JHA presented in the previous slides. For example, do you understand what we’ve said about:
- What JHA means?
- The purpose of JHA?
- The benefits of JHA?
- How jobs are selected for JHA and who participates in the process?
- Inspections to identify hazards and risks?
You need to understand all this information in order to fully understand the importance of JHA in our facility.
Let’s continue to the next slide now and identify the steps in the JHA process.
Steps in JHA
- The first step in job hazard analysis is to break the job down into all the simple, discrete tasks that make up the job. This allows you to look at all the hazards involved in performing the job—including hidden hazards and risks.
- Step two is to identify the hazards involved in each task that must be performed to complete the job. Depending on the job, you could end up with a long or short list. Some hazards and risks may be repeated in several or all the tasks that make up the job.
- Step three involves evaluating each hazard so that you can determine what to do about it and how to prevent injuries or work-related illness.
- Step four is to determine safe procedures and protective measures to prevent accidents, injuries, and illness as a result of each hazard or risk.
- And finally, step five has to be done if the current JHA has become outdated because of changes in the job. A JHA might also have to be revised if hazards are eliminated, reduced, or controlled thanks to the previous hazard analysis.
Now let’s continue to the next set of slides and examine each of these steps in more detail, beginning with the breakdown of the job.
Break Down the Job
To break down the job for a JHA, you have to:
- List each discrete task in the order it’s performed; • Describe each action involved in performing each task;
- Consider the conditions under which the job is performed; and
- Think about the safety issues involved at each step in the job.
Identify the Hazards
Next you have to identify all the hazards and risks associated with each of the tasks you’ve listed in step one. These may include:
- Impact, such as from being struck by an object or falling and hitting the ground;
- Penetration by sharp or pointed objects that cause cuts or punctures;
- Being caught between two objects or pinch points, which can cause crushing or amputations;
- Harmful airborne contaminants from solids, liquids, and gases; and
- Repetitive motions and awkward postures, which can cause musculoskeletal disorders, or MSDs.
Identify the Hazards (cont.)
Hazards associated with various tasks might also include:
- Heat or cold;
- Compression, which can cause broken bones, amputations, and other serious bodily damage;
- Optical radiation, which can cause serious eye damage and even blindness;
- Chemical exposures, such as getting chemicals on the skin or in the eyes or accidentally swallowing hazardous chemicals;
- Ionizing radiation, which includes the risk of being exposed to radioactive material; and
- Slippery surfaces which can cause injuries from falls.
Think about the various hazards associated with the different tasks involved in the job you perform.
Evaluate the Hazards
Step three is to evaluate the job hazards you’ve identified in the previous step. When evaluating hazards, you have to ask questions like these:
- Is this a safety or health hazard?
- Could this hazard cause an injury or illness?
- How serious is the risk?
- Is this hazard always present when the job is being performed or is it an intermittent hazard?
Evaluate the Hazards (cont.)
Here are some additional questions to help evaluate the hazards:
- Are the engineering and/or administrative controls currently being used to prevent injuries and illness effective?
- Is the right PPE being used to protect against hazards?
- Is safety training creating sufficient awareness of the hazards and knowledge of the precautions that must be taken to prevent accidents?
- Are the protective measures currently in place adequate or are additional or different measures required to ensure safety?
Can you think of some other useful questions that would help evaluate hazards identified by a JHA?
Determine Safe Procedures and Protections
The fourth step in JHA is to determine safe procedures and protective measures to prevent injuries and illness based on the hazards identified and evaluated in previous steps. Common ways to reduce or eliminate hazards revealed by a JHA include:
- Performing the job differently;
- Reconfiguring the work area or workstations to make them safer;
- Substituting less hazardous materials;
- Changing from manual to mechanical techniques to reduce the exertion required to perform the job and prevent stress and strain injuries; and
- Insulating or cleaning surfaces.
Determine Safe Procedures (cont.)
Other ways to deal with job hazards include:
- Adding, improving, or changing safety training;
- Changing tools or equipment;
- Changing or adding PPE; and
- Performing the most hazardous tasks less often.
Think about changes in procedures and protective measures that can result from JHAs and how those changes can help make your job safer. Can you think of other steps we might take as a result of a JHA to make your job safer?
Revise the JHA
The last step in the hazard analysis process is to review and revise a JHA any time one of the items listed on the screen occurs. For example, a JHA will be reviewed and may be revised:
- When an accident, injury, or work-related illness occurs;
- After a near miss;
- When the job changes, introducing the possibility of new or different hazards;
- Following an employee safety complaint;
- When equipment is damaged; or
- According to a scheduled, routine review, such as once every 6 or 12 months.
Perhaps you can think of some examples of when a JHA has been revised.
Control Method Hierarchy
In general, when taking steps to deal with job hazards, we follow a control method hierarchy recommended by OSHA.
- We begin by implementing engineering controls to eliminate or reduce the hazards and risks. Ventilation and machine guards are good examples of engineering controls.
- If engineering controls alone can’t eliminate the hazards or risks, or can’t effectively be used, we next rely on administrative controls such as training, safe work practices, job rotation, and so on to reduce the risk of exposure.
- Finally, if engineering and administrative controls can’t completely ensure your safety, you need to wear appropriate PPE to provide a personal barrier between you and the hazards you face when you perform your job.
Exercise
Now let’s see if you can remember the order in which the steps in JHA are performed. Take a minute and decide the correct order of these tasks.
- How did you do? Did you arrange them in the right order?
JHA Steps
Let’s take some time now to make sure you understand the information presented in the previous slides about the JHA process. Do you understand:
- How to break down a job for JHA?
- How to identify hazards in each step of a job?
- How to evaluate hazards identified?
- How to determine safe procedures and protections?
- When a JHA should be revised?
It’s important to understand the process so that you can contribute to the success of any JHA in which you’re involved.
Now let’s conclude the session with some key points to remember.
Key Points To Remember
Here are the main points to remember from this session on job hazard analysis:
- JHA is an essential part of any effective safety program.
- You should be familiar with the purpose and process of JHA.
- Your participation in JHA is important and can help keep you and your coworkers safer on the job.