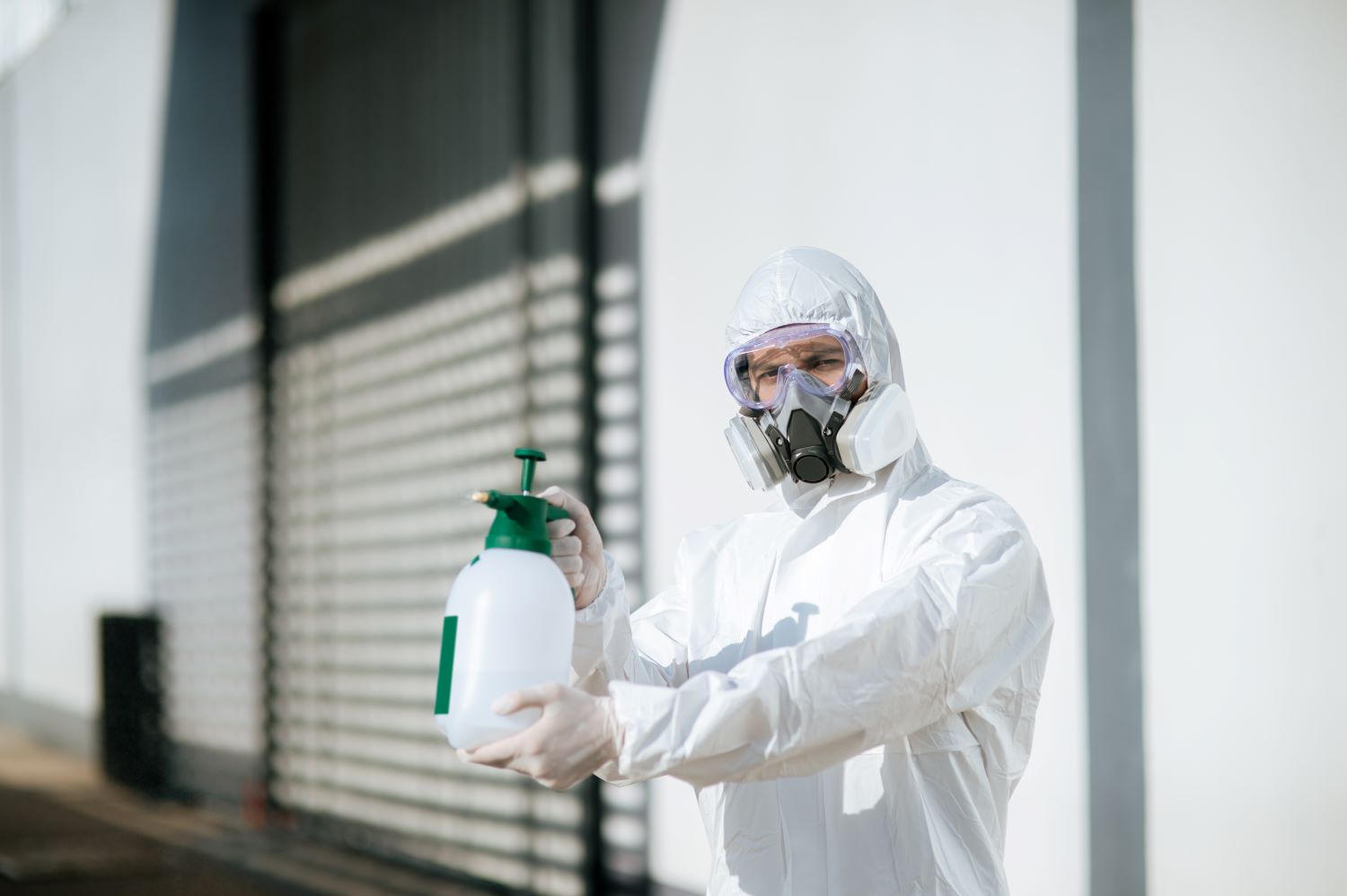
Today, we’re going to talk about a very important workplace safety and health topic—industrial hygiene. You’ll learn what industrial hygiene is and how it helps protect you from workplace hazards.
Table of Contents
Session Objectives
The main objective of this session is to introduce you to industrial hygiene and explain its importance to your safety and health. By the time the session is over, you should be able to:
- Understand what industrial hygiene is;
- Recognize its importance in the workplace;
- Identify ways industrial hygiene helps protect you; and
- Help promote industrial hygiene on the job.
Pre-quiz: True or False?
Before we begin the session, let’s take a few minutes to see how much you already know about industrial hygiene. Decide whether each statement on the screen is true or false.
- Industrial hygiene is primarily about cleanliness and sanitation—false.
- Industrial hygiene has little effect on most people’s jobs—false.
- Industrial hygiene is entirely a management issue—false.
- Industrial hygiene primarily involves hazards that affect your health— true.
How did you do? Did you get all the answers right?
If not, don’t worry. You’ll learn all about these issues and a lot more during the session.
What Is Industrial Hygiene?
Industrial hygiene is the science of anticipating, recognizing, evaluating, and controlling workplace conditions that could cause injury or illness.
Industrial hygienists use environmental monitoring and analytical methods to detect the extent of your risk and exposure to occupational health hazards. Then they use engineering and work practice controls as well as other methods to control potential hazards and risks.
Are you familiar with our industrial hygiene program and the steps we take to protect your health on the job?
Is IH New to the Workplace?
Industrial hygiene, or IH as we’ll call it for the rest of the session, is nothing new to the workplace. People have been aware of industrial hygiene for centuries.
- In the early 20th century in the United States, Dr. Alice Hamilton led efforts to improve industrial hygiene. She observed industrial conditions firsthand and startled mine owners, factory managers, and state officials with evidence that there was a correlation between worker illness and their exposure and the risks posed by their work environment. She also presented definitive proposals for eliminating unhealthful working conditions.
- At about the same time, U.S. federal and state agencies began investigating health conditions in industry.
- In 1908, the public’s awareness of occupationally related diseases stimulated the passage of compensation acts for certain civil employees. States passed the first workers’ compensation laws in 1911. And in 1913, the New York Department of Labor and the Ohio Department of Health established the first state industrial hygiene programs.
- All states enacted such legislation by 1948. In most states, there is some compensation coverage for workers contracting industrial illnesses.
What Is the Connection Between IH & OSHA?
Today, nearly every employer is required to implement the elements of an industrial hygiene and safety, occupational health, or hazard communication program and to be responsive to the Occupational Safety and Health Administration, OSHA, and the Occupational Safety and Health Act and its regulations.
Under the law, OSHA develops and sets mandatory occupational safety and health requirements applicable to the more than 6 million workplaces in the United States. OSHA relies on, among many others, industrial hygienists to evaluate jobs for potential health hazards.
Developing and setting mandatory occupational safety and health standards involve determining the extent of employee risk and exposure to hazards and deciding what is needed to control these hazards, thereby protecting the workers. Industrial hygienists are trained to anticipate, recognize, evaluate, and recommend controls for environmental and physical hazards and risks that can affect the health and well-being of workers.
What Is the Connection Between IH & OSHA? (cont.)
- More than 40 percent of the OSHA compliance officers who inspect America’s workplaces are industrial hygienists.
- Industrial hygienists also play a major role in developing and issuing OSHA standards to protect workers from health hazards associated with toxic materials, biological hazards, and harmful physical agents.
- They also provide technical assistance and support to the agency’s national and regional offices.
- OSHA also employs industrial hygienists who assist in setting up field enforcement procedures, and who issue technical interpretations of OSHA regulations and standards.
- In addition, industrial hygienists analyze, identify, and measure workplace risks, hazards or stressors that can cause sickness, impaired health, or significant discomfort in workers through chemical, physical, ergonomic, or biological exposures. Two roles of the OSHA industrial hygienist are to spot those conditions and help eliminate or control them through appropriate measures.
How Does IH Help Protect You on the Job?
According to the American Industrial Hygiene Association, the science of industrial hygiene and its practitioners, industrial hygienists, help protect you by:
- Investigating and examining the workplace for hazards and potential risks;
- Making recommendations on improving the safety of workers and the surrounding community;
- Conducting scientific research to provide data on possible harmful conditions or risks in the workplace;
- Developing techniques to anticipate and control potentially dangerous situations in the workplace and the community;
- Training and educating employers and workers about job-related risks;
- Advising government officials and participating in the development of regulations to ensure the health and safety of workers and their families; and
- Ensuring that workers are properly following health and safety procedures.
Which Health and Safety Issues Does IH Cover?
Industrial hygiene deals with workplace safety issues from air quality to the hazardous materials regulated by Subpart Z of the OSHA regulations. Included in the other important issues IH covers are:
- Asbestos;
- Biological and radiation hazards;
- Carbon monoxide;
- Ergonomics;
- Mold;
- Noise;
- Occupational diseases;
- Reproductive hazards;
- Temperature; and
- Vibration.
Think about the health hazards of your job and in the workplace—hazards industrial hygiene helps control.
Quiz: Choose the Right Answers
Now let’s try a quiz to test your understanding of the information we’ve just discussed concerning industrial hygiene. To complete this quiz, you have to decide which of the choices for each question are correct. Remember that there could be more than one right answer to each question. You can begin now.
Let’s review quickly.
- Industrial hygiene is the science of anticipating, recognizing, evaluating, and controlling workplace conditions that could cause injury or illness.
- Industrial hygiene covers all three of the choices in the second question.
How did you do? Did you get all the answers right?
Review
Now it’s time to ask yourself if you understand all the information about industrial hygiene presented so far. For example, do you understand what we’ve discussed about:
- What industrial hygiene is?
- The connection between industrial hygiene and OSHA?
- How industrial hygiene helps protect you on the job? • The health and safety issues industrial hygiene covers?
You need to understand all this information in order to understand how industrial hygiene helps keep us all safe and healthy on the job.
Let’s continue to the next slide now and talk about how industrial hygiene helps identify workplace hazards.
How Are Workplace Hazards Identified?
- A worksite analysis is an essential first step that helps an industrial hygienist determine what jobs and workstations are the sources of potential problems.
– During a worksite analysis, the industrial hygienist measures and identifies exposures, problem tasks, and risks.
– The most effective worksite analyses include all jobs, operations, and work activities. The industrial hygienist inspects, researches, or analyzes how particular chemicals or physical hazards at that worksite affect worker health.
If a situation hazardous to health is discovered, the industrial hygienist recommends the appropriate corrective actions.
How Does IH Control Workplace Hazards?
- Industrial hygienists recognize three controls that are the primary means of reducing employee exposure to occupational hazards. They are:
– Engineering
– Work practice, and
– Administrative controls
Engineering Controls
- Engineering controls minimize employee exposure or risk by either controlling, reducing, or removing the hazard at the source or isolating the worker from the hazard.
- Engineering controls include eliminating toxic or hazardous materials and replacing with less hazardous ones, enclosing work processes or confining work operations, and installing general and local ventilation systems.
Think about the engineering controls used in your work area to protect you from health hazards.
Work Practice Controls
Work practice controls alter the manner in which a task is performed. Some fundamental and easily implemented work practice controls include:
- Following proper procedures that minimize exposures while operating production and control equipment;
- Inspecting and maintaining process and control equipment on a regular basis;
- Implementing good housekeeping procedures;
- Providing appropriate supervision; and
- Mandating that eating, drinking, smoking, chewing tobacco or gum, and applying cosmetics in regulated areas be prohibited.
Think about the safe work practices you are required to follow and how they help protect you from health hazards on the job.
Administrative Controls
- Administrative controls include controlling employee exposure by scheduling production and workers’ tasks, or both, in ways that minimize exposure levels. For example, the employer might schedule operations with the highest exposure potential during periods when the fewest employees are present.
- When effective work practices and/or engineering controls are not feasible to achieve the permissible exposure limit, personal protective equipment is required. PPE such as gloves, safety goggles, respirators, hard hats, safety shoes, and protective clothing may be required.
- To be effective, PPE must be individually selected, properly fitted and periodically refitted, conscientiously and properly worn, regularly maintained, and replaced as necessary.
Think about any administrative controls that apply to your job and how these controls help protect you. Also think about the PPE you are required to wear and how it helps protect you from health hazards.
Examples of Job Hazards
To be effective in recognizing and evaluating on-the-job hazards and recommending controls, industrial hygienists must be familiar with the hazards’ characteristics. Potential hazards can include:
- Air contaminants,
- Chemical hazards,
- Biological hazards,
- Physical hazards, and
- Ergonomic hazards.
Let’s take a look at each one of these.
Air Contaminants
Air contaminants can exist as solids, liquids, or gases. The most common are:
- Dusts—solid particles generated by handling, crushing, grinding, colliding, exploding, and heating materials like rock, metal, wood, and grain. Dusts can be seen by the naked eyes, and they can be filtered out by the lungs.
- Fumes—formed when material from a solid condenses in cool air. Fumes may not be seen by the unaided eye and can get deep into the lungs.
- Mist—a liquid suspended in the atmosphere. Mists can be seen and can be caught by the lungs or can be absorbed into the skin.
- Vapors—created by evaporation. They cannot be seen and can easily be absorbed into the body.
- Fibers—solid particles which are generally long and thin. Fibers can get deep into the lungs and can cling and irritate.
- Gases—formless fluids that expand to occupy the space they are in. Gases can be absorbed into the body.
Hazards Due to Chemical Properties
Workers can be exposed to many types of risks due to chemical properties of a material through breathing, direct contact with the skin, or by ingesting. Some of these materials can be simply irritating, or some can be toxic. The degree of risk to the worker depends on several factors:
- The nature and potency of the material,
- The magnitude and duration of exposure, and
- The route of entry.
Information about the risk to workers can be found on the safety data sheet, which is supplied by the manufacturer.
Biological Hazards
Biological hazards include:
- Bacteria,
- Viruses,
- Fungi, and other living organisms that can cause infections, allergic reactions, and illnesses by contact with, or entering the body.
Occupations that deal with plants, animals, food, or food processing may expose workers to biological hazards, as well as the medical field. Using proper PPE, as well as handwashing are good practices to curb the risk of exposure.
Physical Hazards
Physical hazards include levels of:
- Ionizing and nonionizing radiation,
- Noise,
- Vibration,
- Illumination, and
- Temperature.
Limiting the exposure time and distance to these hazards is one way to reduce risk. Also, using engineering controls, such as quieting walls and equipment, and shields can help.
Ergonomic Hazards
Ergonomic hazards include:
- Eye strain,
- Repetitive motion injuries, and
- Lifting injuries.
These hazards can be avoided by using better-designed tools and equipment that meet workers’ needs. Beginning with a worksite analysis, employers can set up procedures that include redesigning workspaces, teaching about good work practices like proper lifting, using administrative work controls such as rest breaks and, if necessary, providing PPE to help control these hazards.
How Can You Promote a Safe & Healthy Workplace?
You can help promote a safe and healthy workplace by taking five simple steps:
- One, report risks and hazards right away;
- Two, cooperate in investigations and inspections, and with monitoring, testing, and medical evaluation programs;
- Three, use engineering controls when necessary to control workplace hazards;
- Four, wear and properly maintain assigned PPE; and
- Five, always follow safe work practices.
Quiz: True or False?
It’s time now for a short true/false quiz to test your memory of the information we’ve just covered about industrial hygiene. Read each of the statements on the screen and decide whether it’s true or false.
Let’s review quickly.
- The first statement is false—IH identifies workplace hazards by conducting a worksite analysis.
- The second statement is also false—Engineering controls protect you by removing or minimizing hazards.
- The third statement is false—Work practice controls primarily involve work procedures, work rules, and supervision.
- The last statement is true—PPE is required when engineering, work practice, or administrative controls alone can’t protect you from health hazards.
How did you do? Did you get all the answers right?
Review
Let’s take a moment now to review and make sure you understand the information presented in the previous slide. For example, do you understand what we’ve said about:
- How industrial hygienists identify workplace hazards?
- How industrial hygiene helps control workplace hazards?
- How you can help promote industrial hygiene in our facility?
It’s important for you to understand all this information so that you can help us protect your health and safety on the job.
Now it’s time to proceed to the next slide and some key points to remember about this training session.
Key Points to Remember
Here are the main points to remember about this training session on industrial hygiene:
- Industrial hygiene plays an important role in your health and safety on the job.
- By identifying and evaluating workplace health hazards, we can control them to prevent injuries and illness.
- Do your part to promote a safe and healthy workplace by reporting hazards and following safety rules at all times.
This concludes the Introduction to Industrial Hygiene training session.