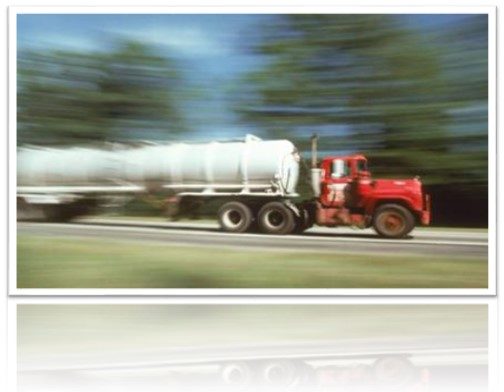
Welcome to the training session on the transportation of hazardous materials. Hazardous materials to be transported are known as “HAZMAT.”
Table of Contents
Who Is a HAZMAT Employee?
You are considered a “HAZMAT employee” and must take this safety training if you perform any of the following job tasks:
- Load, unload, or otherwise handle hazardous materials. Examples include:
– Choose proper packaging;
– Mark or label packages;
– Affix placards; and
– Fill out shipping papers and manifests.
- Operate the vehicle that will be used to transport the hazardous materials; and
- Are likely to be exposed to hazardous materials if there is an accident.
Session Objectives
By the end of the training session, you will be able to:
- Recognize and identify hazardous materials;
- Understand HAZMAT container markings, labels, and placards;
- Load and unload hazardous materials safely;
- Use protective procedures and equipment;
- Avoid accidents with hazardous materials;
- Respond to an emergency; and
- Recognize and respond to security threats.
Recognize Hazardous Materials
HAZMAT employees must know how to recognize and identify hazardous materials. Follow these steps:
- Read the container label to determine if a material is hazardous. OSHA requires all hazardous materials to be labeled with information that includes hazardous components and health effects. – DOT, or Department of Transportation, labels will also tell you if the material is considered hazardous according to DOT. Labels such as “Flammable Liquid,” “Poison,” and “Corrosive” are intended to help HAZMAT employees identify hazardous materials.
- The Occupational Safety and Health Administration, or OSHA, also requires manufacturers of chemicals to provide material safety data sheets, or SDSs, for hazardous materials. Review the SDS to determine the type of hazard.
- It is important that you become familiar with the hazardous materials that are commonly shipped from or received into your workplace.
Review Shipping Documents
You also need to review shipping documents. These documents must have the basic shipping description for the hazardous material, which includes:
- The proper shipping name, which can be found by looking at column 2 of the Hazardous Materials Table (49 CFR 172.101). Look for the name of the chemical or hazardous material that you are shipping in order to find the proper shipping name. If the material is not specifically listed by its technical name, use a generic shipping name, such as “Environmentally Hazardous Substance.”
- The hazard class, which can be found in column 3 of the Hazardous Materials Table.
- The identification number, which can be found in column 4 of the Hazardous Materials Table.
- And finally, the packing group, which can be found in column 5 of the Hazardous Material Table.
Make sure you know how to read the shipping papers and the Hazardous Materials Table in 49 CFR 172.101 for the hazardous materials your facility handles.
Identify Hazard Classes
You need to understand the hazard classes of items that you handle. For example:
- Hazard class 1: “Explosives” is divided into six divisions and includes materials such as ammunition, cartridges, detonators, black powder, fireworks, primer caps, rockets, grenades, and igniters.
- Hazard class 2: “Gases” is divided into three divisions and includes flammable gas such as propane, nonflammable gas such as nitrogen, and gas poisonous by inhalation such as chlorine.
- Hazard class 3: “Flammable or Combustible Liquids” includes gasoline, acetone, oil, paint, etc. Materials with a flashpoint t <1400F are considered flammable. Materials with a flashpoint between 1400F and 2000F are considered combustible.
- Hazard class 4: “Flammable Solids” includes solids such as nitrocellulose, spontaneously combustible solids such as phosphorous, and dangerous-when-wet solids such as sodium and calcium.
Identify Hazards Classes (cont.)
Further classifications include:
- Hazard class 5: “Oxidizer and Organic Peroxide” are materials that enhance the combustion of other materials.
- Hazard class 6: “Poison” includes materials that are inhalation hazards as well as materials that should be stored away from food products. Poisonous materials include arsenic, cyanide, and pesticides. They also include infectious substances.
- Hazard class 7: “Radioactive Materials” can cause burns and other types of injury.
- Hazard class 8: “Corrosive Material” includes acids, caustics, and other materials that destroy human tissue and eat through metals.
- And finally, hazard class 9: “Miscellaneous Hazardous Material” is hazardous material that does not fit into any of the first eight hazard classes and includes asbestos, dry ice, lithium batteries, elevated temperature material, hazardous waste not meeting the criteria of Hazard Classes 1-8, etc.
Find Identification Numbers
Make sure you find the identification numbers:
- The identification number is a specific number that is assigned to each shipping name. For example:
– The “UN” indicates that the material is appropriate for international as well as domestic transportation.
– The “NA” indicates that the material is appropriate only for domestic and Canadian transportation.
– The “ID” indicates shipping names that are recognized by ICAO, or International Civil Aviation Organization or Technical Instructions.
- Placards located on vehicles contain the identification number.
– Emergency responders use the identification number that is located on the placards to determine from a safe distance what type of material they are responding to.
Identify Packing Groups
Know how to identify packing groups, which are assigned according to their shipping name and hazard class and indicate the degree of danger the material presents. Here are the ratings:
- Packing group I indicates a great danger,
- Packing group II indicates a medium danger, and
- Packing group III indicates a minor danger
Read Labels and Placards
Always read warning labels and placards. They contain vital information.
- Warning labels and placards are carefully designed and color-coded so that the hazards can be quickly recognized. Required warning labels can be found in column 6 of the Hazardous Materials Table in 49 CFR 172.101.
- Warning labels include both the hazard class and the division of the hazard.
- Placards are used to alert the public to the potential dangers of hazardous materials transported by road, rail, water, or air. Placards are used to guide emergency personnel in their actions during a HAZMAT incident. Placards correspond to the warning labels that are placed on each individual container.
- Placards must be located on all four sides of the transportation vehicle.
Make sure you’re familiar with the labels and placards that appear on containers and vehicles handled in your facility.
Un-Approved Packages
Here’s what you need to know about UN-approved packages:
- Packages must meet certain requirements before they are permitted to carry hazardous materials. Tests include a drop test, stacking test, vibration test, leakproof test, and a hydrostatic pressure test.
- Once the package passes the appropriate tests, it is marked or embossed with the UN packaging nomenclature, which will start with the letters UN and then have various other numbers, depending on the type of package. For example, a steel drum with a non-removable head designed for packing groups II and III and made in the United States in 2001 would have the following nomenclature: UN1A1/Y1.4/150/01USA.
- Column 8 of the Hazardous Materials Table refers to different sections of 49 CFR 173, depending on the type of hazardous material that is being shipped. Refer to the appropriate section in order to determine what type of package is appropriate for shipping your hazardous material.
- Packages cannot be damaged. They cannot have dents, holes, bulges, or other types of damage.
Make sure you can recognize UN-approved packages, such as drums, boxes, barrels, jerricans, and bags.
Identifying Hazards and Labels – Any Questions?
Now it’s time to ask yourself if you understand the information presented so far.
- Do you understand hazardous materials identification?
- Do you understand how to read labels, markings, or placards?
It is important for your safety that you understand how to read hazardous materials information to determine the hazards you face.
Loading or Unloading Trucks
Here’s what to do when loading or unloading HAZMAT cargo from trucks or transferring liquids in tank trucks:
- Check the safety guide before you begin loading or unloading;
- Remove the ignition keys before loading/unloading to avoid “pull-away” incidents;
- Be careful not to overfill or overload tanks; and
- Be careful when handling cylinders and packages of hazardous materials.
Loading or Unloading Trucks (cont.)
Also, take these precautions when loading or unloading HAZMAT cargo from trucks or transferring liquids in tank trucks:
- Handle empty drums with the same caution as full drums.
- Do not overload closed cargo spaces; allow air to circulate.
- Close all access flanges and valves before moving and allow adequate relaxation time.
Make sure you follow these and your facility’s specific loading and unloading procedures.
Loading and Unloading A Tank Truck or Railcar
Take these precautions when unloading or loading a railcar or tank truck:
- Inspect the vehicle to make sure it is safe before you begin. Check that valves are closed. Make sure there are no visible leaks or signs of leaks. Check that the brakes are applied, wheels are chocked, and caution signs are posted.
- Wear personal protective equipment, or PPE, that is appropriate for the type of chemical you are handling. • Follow the exact unloading or loading sequence as described in your company’s procedures. • Stay in the area during the loading or unloading process. Do not leave without a qualified replacement. Continually check the tank truck or railcar, hoses, fittings, etc., for any signs of leaks.
- Know how to shut down the loading or unloading process in an emergency. Your system may have engineered valves or other emergency shut-down systems. Tank trucks have emergency shut-downs on both the rear and the front of the truck.
- When the loading or unloading process is complete, there are a number of tasks to do, including clearing the hose or line of any chemicals, removing the hose, shutting valves, securing covers, removing signs and wheel chocks, checking placards, etc.
Follow your facility’s loading and unloading checklists.
Handle Drums And Totes Safely
Here’s how to handle drums and totes safely:
- Inspect the drums or totes for any signs of damage, spills, leaks, etc., before unloading them from a truck or before loading them into a truck.
- Make sure the containers are properly labeled and have the appropriate markings, including shipping name, address, etc.
- Carefully remove containers from trucks or load containers into trucks using forklifts, drum attachments for the forklift, drum dollies, or whatever method is used in your workplace.
- Know what to do in an emergency in case a drum, tote, or other small container of hazardous material ruptures or becomes damaged during the unloading process.
- When unloading, place the container in its proper storage area right away. Do not leave hazardous materials on the loading/unloading dock.
Operate a Forklift Safely
For those of you who are certified to operate a forklift, this is a refresher for operating safely. These procedures are outlined in your copy of the Powered Industrial Truck Program.
- Only authorized operators can use a forklift;
- Report all forklift-related accidents;
- Always wear the seat belt;
- Standing under elevated forks may be deadly if the hydraulic system fails;
- Only operate the forklift from the driver’s seat; and
- Don’t block exits or emergency equipment with a forklift.
Make sure you know and follow the operating rules for forklifts used in your facility.
Loading and Unloading With a Forklift
Follow these precautions when loading and unloading a forklift:
- Never attempt to lift or carry a load beyond the rated capacity on the nameplate.
– Check the weight of the load. Placing a weight on the back of a forklift to increase load capacity is extremely dangerous. Obviously, if this happens, the forklift is trying to lift a load over its capacity. Also, adding weight to the back of the lift truck does not increase the capacity of the mast, hydraulic system, chains, or tilt cylinders.
– Locate the load’s center of gravity.
- Inspect the load for stability, projections, and damaged pallets before lifting.
- Restack unstable loads, and secure the load with straps, ropes, or other means of containment if necessary to ensure stability. With wide loads, spread the forks apart as far as possible so that the load will fall inward in case it becomes unstable.
- Never drill a hole in the forks to use as a way of towing something or as a place to put a chain hook when hoisting. This ruins the integrity of the forks. Forklifts are equipped with a tow bar in the back for towing. Safe attachments can be purchased for use when hoisting.
Personal Protective Equipment (PPE)
JOAN:
Protect yourself from the hazards of the materials that you load or unload.
- Review SDSs, labels, and workplace safe work practices to determine what PPE should be worn. Then wear it! For example:
– Most workplaces require the use of eye protection such as safety glasses when loading and unloading any type of material, whether drums or railcars. A face shield may be required when loading/unloading bulk materials from a tank truck or railcar.
– Gloves are also required for almost every loading/unloading operation from drums to railcars. Be sure to wear gloves that are appropriate for the chemical you will be handling.
- Respiratory protection may also be required for loading/unloading chemicals that have a high inhalation hazard.
- Protective clothing and boots should also be worn when handling hazardous materials that present severe skin hazards and when loading/unloading bulk chemicals from railcars or tank trucks.
Make sure you wear the appropriate PPE for the materials you handle in your facility.
Emergency Response To a Spill or Leak
Here’s what you need to know about emergency response to a spill or leak:
- HAZMAT employees must know how to stop the unloading or loading process. Railcars and tank trucks have special ways to shut their internal valves that will stop the flow of material when unloading. The loading and unloading process at your workplace may have emergency valves that can be used to shut down the process. Containers such as drums can be turned such that the hole is facing up and no more material leaks out.
- Evacuate the immediate area, especially if the material is a serious health hazard.
- Alert others by sounding alarms, yelling, or using a paging system. This alarm should also call for the trained emergency response team.
- Respond to the spill or release with spill control and cleanup equipment only if you are authorized and a trained member of the spill response team. Do not attempt to respond to a spill by yourself even if you’re part of the spill response team—wait for the rest of your team.
Know and follow your facility’s emergency response procedures.
Emergency Contacts
Here are the phone numbers that should be readily available in all areas of the company:
- Fire department
- Police department
- Ambulance
- Medical clinic
- Hospital
Make sure you know where to find these numbers quickly in case of emergency. Also, know and follow your facility’s emergency notification procedures.
Rescue and Medical Treatment
Here are important basic procedures for rescue and medical treatment:
- If a worker is trapped or badly injured, leave the rescue work to trained and certified first responders.
- If you or a co-worker is injured, provide medical help for which you are trained. Whenever possible, alert designated first-aid providers or medical personnel to your needs or the needs of co-workers.
- Follow the company’s written medical emergency procedures.
Extinguishing Equipment
Here are the three primary categories of fire-extinguishing equipment:
- Portable extinguisher
- Fire hose
- Fire suppression systems
Make sure you know which fire-extinguishing equipment is used in your facility and where it is located.
Extinguisher Types
DAVE:
Here are the four types of extinguishers based on the kinds of fires they extinguish:
- “A” extinguishers, used for combustibles such as trash, wood, or paper, must be located so that the travel distance for employees to the extinguisher is 75 feet or less.
- “B” extinguishers, used for flammable liquids or gases, must be located so that the travel distance for employees to the extinguisher is 50 feet or less.
- “C” extinguishers, used for electrical fires, are grouped with either an “A” or “B” class extinguisher, so its location is based on the pattern required by the extinguisher class it is grouped in.
- “D” extinguishers, required in areas where combustible metal powders, shavings, or similarly sized products are generated at least once every 2 weeks, must be located so that the travel distance for employees to the extinguisher is 75 feet or less.
- “K” extinguishers will be found in commercial cooking operations such as restaurants. These are wet chemical fire extinguishers that contain a potassium acetate-based, low pH agent. Travel distance to K extinguishers must not exceed 30 feet.
Check OSHA regulation 29 CFR 1910.157 for the distances fire extinguishers must be located from employees. Also, make sure you know if your local fire department has different requirements.
Extinguisher Use
These four steps for using fire extinguishers are easy to remember by thinking about the word PASS:
- Pull the pin.
- Aim at the base of the fire.
- Squeeze the trigger.
- Sweep back and forth.
Most extinguishers are emptied in less than 1 minute, so aim carefully.
Make sure you know how to operate the extinguishers used in your facility.
HAZMAT Safety and Emergencies – Questions?
Now it’s time to ask yourself if you understand the information presented in this section.
- Do you understand how to load, unload, and handle hazardous materials?
- Do you know how to respond to emergencies?
- Do you understand how to use a fire extinguisher?
It’s important for your safety that you know how to handle hazardous materials and how to respond to emergencies, including fires.
Security Plan
Here’s what you need to know about HAZMAT transportation security plans:
- The transportation security plan will be different for every company and every facility within a company. The plan will vary depending on the level of threat, the type and amount of hazardous materials, and potential security risks at each facility or location.
- The plan must include an assessment of possible transportation security risks for shipments of hazardous materials and measures that will be taken to address the risks that were found.
- The security plan will describe how your company confirms information provided by job applicants who are hired for positions that involve access to and handling of the hazardous materials.
- The plan will discuss measures taken to prevent unauthorized persons from gaining access to the hazardous materials.
- Finally, the security plan will also describe measures taken to address potential security risks of shipments of hazardous materials while they are en route to their destination, including shipments that are stored incidental to movement.
Make sure you understand and follow your facility’s transportation security plan, if the facility has one.
Potential Security Risks
Here’s how to determine potential security risks:
- Start by making a list of hazardous materials that you ship or receive that are subject to the security plan requirements. Make the list comprehensive and include radioactive materials, explosive materials, materials that are poisonous by inhalation, and other hazardous materials that require placarding. The more hazardous the material, the greater the security risk. Put the most hazardous materials at the top of your list.
- Consider the quantity of each material that you store at your facility as well as how much you ship or receive at a time. The greater the quantity, the greater the security risk. Chemicals in large bulk quantities require extra security precautions.
- Consider what your chemical shipping and receiving area is like. Your facility may be at a higher security risk if located close to dense populations of people, water supplies, power stations, or sensitive environmental areas.
- Finally, consider the mode of transportation. Shipping and receiving bulk quantities by railcar is probably a greater risk than shipping and receiving smaller quantities by tanker trucks.
Address En Route Risks
Here’s how to address en route risks:
- En route security risks should be addressed both by the carrier or transporter as well as the shipper. Select carriers that have security plans developed and implemented, understand the hazards of the materials being shipped, have secure storage areas, and secure delivery routes.
- Assess loading and unloading areas and procedures for security risks including emergency shutdown, loading and unloading equipment, and access by unauthorized personnel.
- Assess your methods of dispatching loads. Can unauthorized persons find out when your loads of hazardous materials will be picked up, what route they are taking, or where they are going?
- Finally, assess the security of the destination of your hazardous materials. If they are being shipped to another facility with a security plan, your load will probably be safe. However, if the load is going to an unsecured area or location, assess the security risks associated with shipping hazardous materials to that destination.
Secure Hazardous Material
Take these steps to secure hazardous materials that are stored at your facility:
- Keep access to storage areas locked.
- Conduct frequent and accurate inventories. A good inventory will help you determine if materials are being stolen.
- Conduct regular inspections of chemical storage areas. Check doors, fences, gates, etc., to ensure the area is properly secured. Inspect pipes, tanks, drums, and other containers for any signs of damage. Look for anything that is unusual or out of the ordinary.
- From customers, look out for unusual chemical purchases that are larger than normal quantities or from unknown customers. Also, keep an eye out for odd behavior from customers, truck drivers, or your own employees.
- Finally, check driver identification. Write the driver’s license number on the shipping paperwork or bill of lading and have the driver print and sign his or her name. Verify that the driver has the proper hazardous materials endorsement.
Make sure you know and follow your facility’s security procedures in hazardous material storage areas.
Report Suspicious Personnel or Activities
Identify and report suspicious personnel or activities in the work area— especially when near hazardous chemicals. Here’s what to be aware of:
- A person loitering by chemical tanks, especially when not authorized, is suspicious activity and must be reported.
- Report anyone loitering by loading docks where chemical containers are handled.
- Someone walking along the outside of the security fence should be considered suspicious. The person may be looking for potential access points to the facility.
- Finally, unusual vehicles parked outside your facility could indicate some type of danger, such as someone waiting for a hazardous material shipment to leave your facility so that the truck can be hijacked.
Responding to Security Threats
When you recognize a security threat, such as suspicious persons or a suspicious object or package near hazardous materials, respond with these steps:
- Do not approach suspicious persons or objects;
- Call facility security or the police;
- Warn other employees in the area of the suspicious behavior;
- Secure the area by locking doors and gates; and
- Evacuate the area or shelter-in-place as determined in your company’s emergency response plan.
Make sure you know and follow your facility’s procedures for responding to security threats.
Your Role in Security
Every employee plays a key role in the physical security of the workplace. Do your part and take these precautions:
- Keep doors locked. This includes doors that lead outside as well as internal security doors that prevent access to areas from public hallways or lobbies.
- Do not let others borrow keys or access cards to the building or to your work area. Do not give out access codes or other access information.
- Be careful with strangers. Unauthorized personnel may try to enter a building “on your coattails” by following you through a door after you have used your key or access card to open a door. They may thank you for holding the door open so that they did not have to get out their key. Before letting any people in, require them to show identification or their key to prove they are authorized to be in the building.
- Finally, report unknown personnel in your work area.
Security – Any Questions?
Now it’s time to ask yourself if you understand the information presented so far. Do you understand security risks and procedures for responding to them? It’s important for your safety that you know how to recognize and respond to security risks and threats.
Key Points to Remember
Here are the key points to remember about handling HAZMAT safely:
- Read the shipping descriptions;
- Read and follow label and placard warnings;
- Follow all safe HAZMAT handling procedures—they could save your life;
- Wear proper PPE to avoid injury; and
- Follow security procedures—report suspicious people or activities immediately.
This concludes this training session.